"현대제철㈜"의 두 판 사이의 차이
잔글 |
잔글 |
||
446번째 줄: | 446번째 줄: | ||
* [[현대자동차그룹]] | * [[현대자동차그룹]] | ||
− | |||
{{대기업|검토 필요}} | {{대기업|검토 필요}} |
2021년 8월 10일 (화) 10:21 판
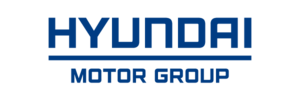
현대제철㈜(Hyundai Steel)은 현대자동차그룹 계열 철강 제조업체이다. 주요 사업은 제철·제강·압연 및 철강재 판매이다.[1]
[타고] 1개월 단위로 전기차가 필요할 때! 타고 월렌트 서비스 |
목차
개요
1953년 대한민국 최초의 철강회사로 시작한 현대제철은 철강산업 발전이 곧 국가경쟁력 강화라는 소명의식을 가지고 수많은 난관을 극복하며 국가 경제 발전에 기여해 왔다. 또한 2010년 민간기업 최초로 일관제철소를 완공함으로써 세계 최고의 제품 포트폴리오를 갖춘 글로벌 철강기업으로 성장했다. 현대제철은 무엇보다 현대자동차그룹의 일원으로 쇳물에서 자동차로 이어지는 그루브이 자원순환형 연결고리에 뼈대 역할을 수행하고 있다. 고로에서 만들어진 현대제철의 쇳물은 자동차가 되고 수명이 다한 자동차는 전기로에서 녹여져 건물의 토대를 이루는 H형강과 철근으로 재탄생한다. 이러한 유기적 자원순환구조는 효율적인 에너지 운용으로 온실가스 감축에 실질적으로 기여하고 있다. 시시각각 변화하는 철강 산업의 경영환경과 높아지는 고객의 기대치 속에서 경쟁력을 갖추고 꾸준한 성장을 이루기 위해 현대제철은 철 그 이상의 가치창조(Engineering the future beyond steel)라는 비전을 목표로 삼은채 고객의 기대를 뛰어넘는 차별화된 가치를 가진 새로운 제품과 서비스를 제공하기 것에 집중하고 있다.[2]
현대제철은 1953년 6월 10일, 6·25전쟁이 채 끝나지 않은 시기에 대한중공업공사로 출발했다. 대한중공업공사는 전후의 시설 복구에 필요한 철강재 생산을 위해 평로 제강공장, 분괴·중형 압연공장, 박판 압연공장 등 생산공장을 연달아 시공했다. 그리고 국내 철강업체 최초의 공채사원을 선발하고 회사 규정 체계를 갖추는 등 빠른 속도로 조직체제를 구축해 탄탄한 경영역량을 기반으로 철강산업을 선두주자로 자리매김했다. 1962년 11월에는 인천중공업으로 사명을 개명하고 1970년 4월에는 인천제철과 합병하여 21세기 현대제철로 확장되는 기반을 마련했다. 1978년 인천제철은 정부 방침에 따라 민간기업에 불하됐다. 이때 현대그룹은 철강사업에 진출한다는 기업방침을 세우고 그룹 차원의 역량을 집중해 인천제철을 인수했다. 현대그룹으로 편입된 인천제철은 경영진 개편과 동시에 새로운 비전과 경영체제를 확립하는 등 과거와는 전혀 다른 위상을 구축했다. 기술적으로도 큰 발전을 이룬 인천제철은 국내업계 최초로 대형 구조물의 골조로 사용되는 H형강을 생산하기도 했다. 이와 같은 노력으로 인천제철은 1993년 매출 1조 원 시대를 열었으며, 1997년 외환 위기에서도 공격적인 경영활동을 펼치게 되는 기반을 다졌다. 외환 위기가 계속되는 위기에서도 인천제철은 공격적인 경영을 통해 강원사업과 삼미특수강을 차례로 인수했다. 강원산업 인수로 인천제철은 800만 톤에 육박하는 생산능력을 보유하게 되어 국내 전기로 제강의 35% 이상을 차지하는 대규모 철강 회사로 거듭났으며, 생산량 기준 세계 2위의 전기로 업체가 됐다. 또한 삼미특수강 인수로 연간 25만 톤의 스테인리스 생산능력을 갖추게 됐다. 이처럼 대규모의 경제를 실현한 인천제철은 2001년 새롭게 출범한 현대자동차그룹의 일원으로 또 한번의 도약을 맞이했다. 이러한 혁신의 일환으로 사명을 INI STEEL COMPANY로 변경해 제2의 창업선언을 했다. 2004년 INI STEEL은 한보철강을 인수한 후, 인수 7개월 만에 열연강판 상업생산에 성공했다. 열연공장 조기 정상화를 이룬 INI STEEL은 곧바로 일관제철소를 시공하면서 국내 최초의 민간 일관제철소 사업에 본격적으로 뛰어들었다. 2006년 사명을 현대제철로 바꾸고 같은 해 일관제철소 기공식을 개최하며 종합철강회사로 나아가고자 하는 의지를 대내외에 표명했다. 2010년 1월, 일관제철소 건설을 시작한지 40개월 만에 제1고로 화입에 이어 같은 해 11월 제2고로에 불씨가 잇따라 지펴졌다. 2013년 9월 제3고로 건설까지 마무리되면서 현대제철은 국내 최초의 민간 자본에 의한 일관제철소를 완공했다. 이로써 현대제철은 연산 1,200만 톤 규모의 고로 3기를 갖추고 열연, 후판을 생산할 수 있게 됐다. 현대제철은 더나아가, 2013년 현대하이스코의 냉연부문을 분할 합병하고, 이후, 2015년 당진에 특수강 공장 건설을 완료하면서 세계 최고의 자동차소재 전문제철소이자 글로벌 철강사로 도약했다.[2]
주요인물
안동일은 현대제철 대표이사이다. 현대제철의 경쟁기업인 포스코에서만 35년 가까이 일한 제철설비분야의 전문가다. 철강산업의 수익성을 회복하는 동시에 수소산업 등 미래 주요 산업을 육성하는데 조직역량을 집중하고 있다. 1959년 5월23일 충청북도 제천에서 태어났으며, 청주고등학교와 부산대학교 생산기계공학과를 졸업하고 캐나다 맥길대학교 대학원에서 경영학 석사학위를 받았다. 이후, 포스코에 입사해 포항제철소 설비기술부 부장, 광양제철소 설비담당 부소장, 포스코 기술위원, 광양제철소 소장, 포항제철소 소장을 역임했다. 포스코 고문으로 일하다 현대제철의 생산·기술부문담당 사장으로 영입되고 얼마 지나지 않아, 대표이사 겸 이사회 의장에 선임됐다. 혁신과 변화를 강조하며 직원과 소통에 힘쓰고 있다.[3]
안동일은 2015년 1월 말 포스코 광양제철소장에 임명됐다.포스코의 포항제철소와 광양제철소 소장이 동시에 바뀌었는데 이는 포스코그룹 창사 이후 처음 있는 일이었다. 2015년 2월2일 열린 취임식에서 위대한 제철소의 실현을 강조하면서 이를 위해 추진할 3가지 경영방침으로 안전, 설비강화, 수익성 향상 등을 강조했다. 안동일은 스스로 안전을 지켜나가는 문화를 정착시킬 다양한 활동을 실행을 강조했으며 임직원들에게 안전과 관련한 다양한 지식을 실천으로 옮기는 자세를 가져줄 것을 당부했다. 구체적으로 자기 주도의 안전 활동인 안전 SSS활동을 통해 직원 스스로가 안전을 지켜나가는 문화가 정착될 수 있도록 다양한 활동을 추진할 것을 약속했다.또한 포스코 고유의 혁신활동을 강화하고 지속적 설비 개선 노력을 통해 독보적 경쟁력을 확보하는데 집중할 것을 강조했으며 수익성 향상을 위해 프로젝트 중심의 일하는 방식을 추진하겠다는 의지를 보였으며, 다각적 원가 절감활동을 통해 재무적 성과를 창출하는 데도 노력하겠다고 각오를 다졌다. 안동일은 실제로 광양제철소장을 역임하면서 설비성능 복원 관련 운영체제 개선, 부서별 낭비요소 제거방안, 업무 몰입도 제고를 위한 실천 등의 여러 방면에서 노력을 기울였다. 본연의 경쟁력을 강화하는 데도 주력했다. 2015년 9월 광양제철소에 고급 자동차강판 전용공장을 대규모 증설하기도 했다. 이는 연간 50만 톤 규모의 용융아연도감강판을 생산할 수 있는 공장으로 포스코를 글로벌 2위 자동차강판 생산 철강기업으로서 입지를 확고히 다질 설비로 평가됐다. 포스코는 이 대규모 설비 증설에 약 2년 동안 2,500억 원이 넘는 자금을 투입했다. 경쟁력을 강화하기 위한 직원 교육활동도 활발히 진행했다. 2015년 10월 원가 절감을 통한 수익성 창출 및 경쟁력 확보를 목표로 철강업의 토요타 실현을 위한 대장정을 기획했다. 다양한 외부 컨설턴트를 초청해 특강을 진행했으며 직접 직원들을 불러 모아 철강업의 도요타 실현을 위한 대토론회를 주관하기도도 했다.[3] 2017년 2월에는 포스코그룹 정기인사를 통해 포항제철소장에 임명됐다. 안동일은 취임사에서 포항제철소의 새로운 50년을 준비해야 하는 중책을 맡아 책임감과 사명감을 느끼며 지난 50여 년의 성장을 발판으로 삼고 유연하고 창의적인 기업문화를 바탕으로 각자의 역량을 최대한 발휘하여 그 어떤 변화와 도전에도 의연히 맞서 위대한 포스코, 위대한 포항제철소의 미래를 새롭게 열어가자고 말했다. 포항제철소 경영방침으로 선제적 안전 예방 활동을 강화해 위험 없는 제철소 구현, 설비 고도화를 통한 설비 본원 경쟁력 강화, WP제품 생산확대를 위한 핵심 고급강 양산제조 기술력 확보, 고장제로(zero), 불량 제로, 낭비 제로의 3대 제로 도전을 통한 수익성 제고 등을 강조했다. 안동일이 포항제철소장에 취임한 직후 포스코는 포항제철소의 설비 고도화에 1조 원이 넘는 돈을 쏟아부었다. 포스코는 2017년 2월 27일, 넥스트(Next) 50년 설비고도화 투자 발대식을 개최하고 노후 설비가 많은 포항제철소 설비 성능을 대대적으로 개편하여 고부가가치 월드프리미엄(WP) 제품 생산을 확대하고 미래 성장동력을 확보하기로 했다. 뿐만 아니라, 품질혁신에도 집중했다. 안동일은 2017년 6월부터 9월까지 100일 동안 고품질 월드프리미엄(WP) 제품을 생산하기 위해 품질혁신 100일 프로젝트를 실시했다. 포항제철소 선재부, 전기강판부, 스테인리스(STS) 3개 부서를 대상으로 품질과 생산성을 대폭 개선해 품질 부적합률을 가능한 50%까지 낮추는 것을 목표로 세웠다. 안동일은 품질 부적합률 50% 저감은 반드시 이룰 수 있다며 포스코의 미래는 월드프리미엄 제품이 좌우한다는 생각으로 모든 직원들이 지속적으로 혁신에 참여해 주기를 바란다고 격려했다.[3]
안동일은 2019년 2월15일 포스코를 벗어나 현대제철에 신설된 생산·기술부문담당 사장에 선임됐다. 현대차그룹은 2019년 철강산업이 글로벌 경기 침체에 따른 수요 감소, 보호무역 기조 강화 등과 함께 중국 기업을 중심으로 글로벌 철강사의 경쟁이 격화하는 추세이기 때문에 철강산업을 둘러싼 경영환경을 극복하는 동시에 기업 경쟁력을 높이기 위한 차원으로 이번 인사를 진행했다. 현대차 그룹은 안동일 사장의 풍부한 경험과 노하우를 바탕으로 현대제철의 당진제철소를 비롯해 생산과 연구개발, 기술품질, 특수강부문 경쟁력을 한 단계 높이는 역할을 맡게 될 것이라고 설명했다. 안동일은 포항제철소장으로 일할 때 선제적 안전 예방과 설비 고도화, 고급강 양산 기술력 확보 등에도 힘썼다. 현대제철이 경쟁기업인 포스코 출신 인사를 사장으로 영입한 것이 파격적 영입이라는 의견이 쏟아졌다. 2001년 현대차그룹이 출범한 뒤 현대제철은 그동안 최고 경영진을 내부에서 발탁하거나 현대차그룹 계열사에서 선임했다. 2006년 일관제철소 건설과 운영 기술을 확보하기 위해 포스코 출신 엔지니어를 대거 영입한 적은 있지만 사장급을 데려온 것은 안동일이 처음이었다. 현대차그룹은 정의선 총괄 수석부회장의 의중에 따라 현대제철의 경쟁력을 강화하기 위해 컨설팅회사를 통해 외부에서 철강 전문가들을 물색했던 것으로 알려졌다. 이후 2019년 3월22일 열린 정기 주주총회에서 안동일이 사내이사에 오르는 안건을 주주들이 승인했다. 안동일은 정기 주주총회가 끝난 뒤 열린 이사회에서 현대제철의 단독 대표이사에 공식적으로 선임됐으며, 이사회 의장도 겸임하게 됐다.[3] 안동일은 2021년 2월 25일, 안동일은 한국철강협회 정기총회에서 비상근 부회장에 재선임됐다. 한국철강협회는 국내 철강산업 경쟁력 강화를 위해 1975년에 만들어진 단체로 포스코, 현대제철, 동국제강 등 국내 주요 철강업체가 회원사로 참여하고 있다. 한국철강협회는 올해 사업 기본목표를 포스트 코로나19 이후 철강산업 활력 제고 및 경쟁력 강화로 정하고 친환경 성장기반 구축, 통상마찰 선제대응 및 수출 확대, 산업 고도화와 연구개발(R&D)활동 등을 중점적으로 추진하기로 했다. 안동일은 2021년 신년사에서 화두로 안전과 환경·사회·지배구조(ESG) 경영을 제시했다. 안동일은 신년사에서 안전은 선택이 아닌 필수사항이며 고위험 작업과 관련한 개선활동을 통해 안전한 작업환경을 조성함과 동시에 임직원 모두가 안전규정을 준수하고 안전활동을 실천하는 자율안전문화를 정착해야 한다고 말했다. 그는 ESG경영을 두고 21세기 기업은 재무적 요소뿐 아니라 환경, 사회, 지배구조 등 비재무적 요소에 따라 지속가능경영의 성패가 좌우되며 모든 임직원이 이런 가치에 한층 깊은 관심과 폭넓은 참여를 기울여야 한다고 설명했다. 안동일은 탄소중립은 철강산업에서도 피할 수 없는 중요한 과제인 만큼 우리의 모든 업무영역에서 탄소배출과 관련한 깊은 고민이 필요하고 탄소중립을 실현하기 위해 각 부문에서 실천과제들을 발굴하고 수행해야 한다고 강조했다 안동일은 2021년 과거 규모의 성장에 치중했던 관성을 청산하고 수익성 중심의 견고한 철강사라는 기업 정체성을 구축해야 한다고 말하며, 수익성 강화를 위한 구체적 전략방향으로는 사업구조 및 설비운영 최적화, 책임경영 강화, 미래 성장기반 확보 등 3가지를 꼽았다.[4]
연혁
- 1953년 06월 10일 : 대한중공업공사 창립
- 1962년 11월 10일 : 인천중공업주식회사로 상호변경
- 1964년 09월 01일 : 인천제철주식회사 설립(양사체제)
- 1970년 04월 01일 : 인천제철로 통합
- 1978년 06월 22일 : 현대그룹에 편입
- 1982년 03월 05일 : H형강공장 조업개시
- 1987년 05월 23일 : 기업공개
- 1990년 09월 15일 : 12만톤 스테인리스 냉연공장 증설 준공
- 1992년 10월 04일 : 국제철강협회 정회원 가입
- 1998년 03월 20일 : 120톤 전기제강공장 및 신 중형 압연공장 준공
- 1999년 12월 02일 : 청도 현대 기계 유한공사 설립
- 2000년 03월 15일 : 강원산업㈜ 인수합병
- 2000년 12월 01일 : 삼미특수강㈜ 인수합병
- 2001년 04월 02일 : 현대자동차그룹으로 출범
- 2001년 07월 27일 : INI STEEL로 사명변경
- 2004년 10월 12일 : 한보철강공업㈜ 당진공장 인수합병식
- 2005년 05월 02일 : 당진 박판열연공장 상업생산 개시
- 2006년 03월 10일 : 현대제철로 사명 변경
- 2006년 10월 27일 : 일관제철소 기공식
- 2009년 09월 02일 : 세계 최초 밀폐형 원료처리시스템 가동
- 2010년 01월 05일 : 일관제철소 1고로 화입식
- 2010년 04월 08일 : 일관제철소 준공식
- 2010년 11월 23일 : 일관제철소 2고로 화입식
- 2011년 04월 12일 : 일관제철소 3고로 기공식
- 2013년 09월 13일 : 일관제철소 3고로 화입식
- 2014년 04월 08일 : 특수강 공장 기공식
- 2015년 07월 01일 : 현대하이스코㈜ 합병
- 2015년 07월 15일 : 비전선포
- 2015년 10월 01일 : 특수강 공장 준공
- 2017년 11월 01일 : 내진강재 브랜드 H CORE 론칭
- 2019년 04월 01일 : 자동차용 철강 솔루션 브랜드 H-SOLUTION 출시
- 2019년 11월 01일 : 내마모강 브랜드 웨어렉스 론칭
- 2020년 09월 01일 : 고강도강 브랜드 울트렉스 론칭[2]
경영철학
현대제철의 심벌 H는 진취적 기상(High Spirit), 조화(Harmony), 인류애(Humanity)를 상징하고, 사명감을 느끼게 한다. H의 견고한 양 축은 현대제철의 신규·과거 사업과 기업, 고객을 뜻하며 가운데 교량(Bridge)은 양 축의 균형적 만남과 통합으로 성장하는 미래를 뜻한다. 블루컬러는 현대제철이 첨단기술과 신뢰를 바탕으로 밝은 미래 환경의 청사진을 구현하는 선도 기업임을 드러낸다. 진취적 기상, 조화, 인류애는 현대제철이 도전적이고 혁신적인 기상과 조화를 통해 밝은 미래사회에 공헌하는 세계 최고의 글로벌 철강기업으로 도약해 나간다는 뜻이다.[2]
- 무한책임 정신 : 고객의 안전과 행복에 대한 무한책임정신은 품질경영으로 구현되며, 우리 사회를 위한 무한가치창조로 이어진다.
- 가능성의 실현 : 하나의 목표달성에 안주하지 않고 늘 새로운 목표를 향해 나아가며, 실패를 두려워하지 않는 도전정신으로 더 큰 미래를 창조한다.
- 인류애의 구현 : 인류를 위한 가치를 기반으로 더 좋은 제품과 서비스를 더 많은 사람에게, 더 신속하게 제공해 인류의 생활을 더욱 풍요롭게 한다.
주요사업
고로사업
고로 공정의 대부분이 화학적 반응으로 구성되어 있다. 화학 지배적인 영역에서는 예외성이 없다. 제철소 사업은 대규모 물류, 전력 생산, 석탄화학, 엔지니어링 등 거의 전 산업 영역에 걸친 기술 학습장이다. 현대제철은 자동차소재 전문제철소로서 미래 자동차를 위한 차세대 강판 개발에 주력하고 있다. 2006년 10월 당진제철소에서 일관제철소 기공식을 개최했으며 2010년 1월과 11월에 각각 제 1ㆍ2고로가 가동됐다. 2013년 9월 당진제철소제3고로 완공을 통해 총 3개의 고로를 가동함으로써 고로 부문 1,200만 톤과 기존 전기로 부문 1,200만 톤을 합쳐 총 2,400만 톤의 조강생산능력을 보유한 글로벌 종합 철강업체로 발돋움했다. 또한, 2013년 12월 현대하이스코의 냉연부문을 합병해 원료에서 최종 제품까지 모든 생산공정을 갖춘 원스톱 생산 체제를 구축했다.[2]
지상 110m 높이로 우뚝 솟아 일관제철소의 상징으로 불리는 고로는 화입과 동시에 생명을 얻고 끊임없이 붉은 쇳물을 토해내는 욕광로 본연의 기능을 발휘하게 된다. 고로는 철광석을 녹여 선철을 만드는 제선공정의 핵심설비로서 소결공장과 코크스공장에서 제조한 소결광과 코크스를 원료로 사용한다. 여기서 나온 쇳물은 다음 공정인 제강공장으로 보내져 불순물을 제거하고 실생활에 사용할 수 있는 강철로 만들어진다. 이후 연속주조공장에서 슬래브(Slab)로 만들어진 뒤 열연공장과 후판공장으로 보내져 최종 제품인 자동차용 열연강판과 조선용 후판으로 탄생한다. 내용적 5,250㎥, 최대 직경 17m, 높이 110m의 대형 크기인 현대제철의 고로는 2010년 당시, 세계 최고 수준의 엔지니어링이 도입된 설비이며, 조업이 정상궤도에 오를 경우 기존 고로에 비해 품질과 가격경쟁력에서 우위를 점할 것으로 기대됐다. 또한 이 고로는 설계 당시 국내 최대 용적으로 설계되었으며 정몽구 회장의 환경경영 철학을 반영해 최신 친환경기술이 적용된 설비로 만들어졌다. 무엇보다 기존 일관제철소와 크게 차별화되는 점은 고로에 장입되는 제철원료를 하역, 이송, 보관하는 시스템이 모두 밀폐형으로 운영되는 전 세계 최초의 녹색제철소라는 것이다. 항만에서부터 철광석과 유연탄 등 제철원료를 밀폐형 연속식 하역기로 하역하고 밀폐형 벨트컨베이어를 이용해 이송함으로써 먼지와 소음을 확실하게 차단할 수 있으며 제철원료를 보관하는 저장고도 완전 밀폐형으로 안전하게 건설되었다. 더불어, 일관제철소 개별 공장에도 설계단계부터 최신의 친환경 설비와 환경오염 방지 기기들을 도입하고 가동함으로서 정부의 녹색성장 정책에 부합되는 세계적인 친환경 경제철소가 본격적으로 가동되었다.[5]
현대제철은 7월 29일 서울 여의도 한국거래소에서 2010년 2분기 실적설명회를 갖고 매출액 2조7,206억원, 영업이익 3,467억원, 당기순이익 1,682억원의 실적을 실현, 고로조업 첫 분기 흑자를 기록하는 예상을 뛰어넘는 성과를 달성했다고 밝혔다. 2분기 경영성과를 살펴보면 매출액은 열연강판 판매증대 및 후판의 신규 시장 진입에 힘입어 전년 동기대비 39.7% 늘었고 영업이익도 156.3% 증대됐다. 당기순이익의 경우 환율상승에 따른 환산손 발생 등으로 전년 동기대비 40.6% 감소했다. 현대제철 관계자는 2분기 경영실적에 대해 건설경기 침체에 따른 봉형강류 판매부진과 원자재 가격 급등 상황을 맞았지만 1고로 조업의 조기 안정에 따른 생산 및 판매 증대, 집중적인 원가절감 노력과 수출단가 및 환율상승에 따른 수출부문의 채산성 증가로 손익개선을 이끌어 냈다고 설명했다. 특히 제철사업 첫 분기에 흑자를 시현한 것은 단위공장별 생산목표 물량을 조기에 초과 달성함에 따라 빠르게 품질을 안정화시킨 것과 기존 A, B열연의 제품개발 실적을 바탕으로 고로재의 강종개발을 조기에 달성했기 때문이었다. 현대제철은 고로 가동 3년 전인 2007년, 기술연구소를 먼저 건립하고 제선, 제강, 연주, 압연 등 일관제철소 공정에 대한 선행연구를 진행했으며 더불어, 독일 등 설비 공급사와 기술 협력사에 현지 연수단을 파견하고 슈퍼바이저 초빙을 통한 기술지도 등을 실시해 제철소의 조기 조업 안정화를 가능하게 했다. 현대제철은 이와 함께 원가절감을 위한 철저한 집중관리를 시행해 기존 봉형강 사업부문에서 저선철 조업, 회수율 개선, 부원료 및 조업자재의 절감 등을 이뤄내고 제철사업에서는 연원료 배합비 개선, 회수율 향상, 에너지 절감 등을 통해 총 1,405억원 수준의 원가절감을 실현했다. 4월부터 본격적인 상업생산을 시작한 후판의 경우에도 꾸준히 생산량을 늘려가고 있으며 9월부터 열처리강 양산체제에 돌입하는 등 2010년 총 49종의 후판 개발 목표 가운데 이미 34개 강종의 개발을 완료하는 성과를 거뒀다. 현대제철은 향후에도 1고로의 안정적인 조업이 이어지고 11월 말 2고로 가동(종합공정률 97.8%)까지 이뤄지면서 고로 2기 운영 체제의 정상화에 따라 강력한 시너지 및 고정비 효과로 수익성 개선은 더욱더 증대될 것으로 예상된다. 한편 현대제철은 대규모 장치산업의 투자를 통해 신규 일자리를 창출하며 국가경제에 이바지했다. 2010년 11월 23일에는 당진제철소의 2고로가 완공됐다. 현대제철은 일관제철사업 착공 직전인 2005년 연말에 비해 고용 증대 인원이 5,800여명에 이르는 것으로 나타났다. 연세대학교 도시교통과학연구소는 지난 2006년 일관제철소 기공 당시 제철소 완공 이후 운영에 따른 직간접 고용창출효과가 7만8,000명에 이를 것으로 추정했다.[6]
자동차소재 전문제철소의 완성을 알리는 현대제철의 3고로 화입으로 우리나라 기간산업이 새롭게 요동치기 시작했다. 현대제철 3고로의 안정적인 조업을 통해 고품질의 철강 소재를 적기에 공급함으로써 경기 침체로 고전하고 있던 건설, 조선, 기계, 자동차 등 우리나라 주력 산업의 글로벌 경쟁력이 크게 향상될 것으로 예상됐기 때문이다. 2013년 9월 13일 현대제철은 당진제철소 제3 고로공장에서 현대차그룹 정몽구 회장과 고로 엔지니어링을 주관한 폴워스(Paul Wurth)사 마크 솔비(Marc SOLVI) 사장 등 내외빈과 임직원이 참석한 가운데 현대제철 당진제철소 제3고로 화입식 행사를 가지면서 성공적인 3고로의 가동을 알렸다. 현대차그룹 정몽구 회장은 이날 기념사를 통해 현대제철은 전 세계적인 경기침체에도 불구하고 지난 7년 동안, 총 9조9천억원의 대규모 투자를 차질 없이 추진해 약 20만 개의 새로운 일자리를 창출하고 지역 경제 발전에 크게 기여해 왔다고 말했으며 또한, 앞으로도 현대제철은 세계 최고의 철강회사를 향한 끝없는 도전을 계속해 나갈 것이며 지속적인 투자와 일자리 창출을 통해 국가와 지역경제 발전에 공헌할 것 이라고 강조했다. 현대제철의 3고로는 기존 1·2고로와 동일한 내용적 5천250㎥, 최대 직경 17m, 높이 110m 규모에 연간 400만 톤의 쇳물을 생산할 수 있는 설비로서 조업이 정상궤도에 오르면 고부가가치 제품 개발 및 생산에 큰 역할을 할 것으로 평가됐다.[7] 현대제철은 2006년 10월 민간기업 최초로 일관제철소 건설에 나서 1ㆍ2고로 건설에 6조2천300억원, 3고로 건설에 3조6천545억 원 등 7년간 총 9조8천845억 원의 투자금을 쏟아부으며, 고로 3기를 갖춘 자동차소재 전문제철소의 대역사를 기록했다. 한국산업조직학회 연구결과에 따르면 현대제철 당진제철소가 건설되는 7년 동안 국내 경제 파급효과도 막대해 고로 투자로 인한 고용창출 효과는 건설과정에서 9만 5,800명, 운영과정에서 11만300명 등 총 20만6,100명에 이르는 것으로 나타났다. 구체적인 생산유발 효과 역시 건설과정에서 21조3,240억 원, 고로 운영과정에서 24조5,570억 원 등 총 45조8,810억 원에 이르는 것으로 나타났다. 또한 현대제철은 3고로 가동을 통해 고로 부문 조강생산능력 1,200만톤 체제를 구축하게 되며 기존 전기로 부문 조강생산능력 1,200만톤을 합쳐 총 2,400만톤의 조강생산능력을 보유한 글로벌 종합 철강업체로 발돋움했다. 전기로에서 생산되는 철근과 H형강 등 건설용 강재 제품은 물론 철강제품의 꽃인 자동차강판과 조선용 후판에 이르기까지 생산 제품도 훨씬 다양해지면서 세계 최고의 제품 포트폴리오를 보유하게 됐다. 조강생산능력 2,400만 톤은 전세계 철강업체 가운데 10위권에 가까운 규모로 세계철강협회 자료에 따르면 2006년 31위에 머물렀던 현대제철은 2010년 일관제철사업을 시작하며 20위로 뛰어올랐고 3고로가 본격적으로 가동되는 2013년 이후에는 세계 11위 규모의 글로벌 철강사로 자리매김하게 됐다. 특히 현대제철의 이러한 대성장은 세계적인 철강업체들이 대형 인수·합병(M&A)을 통해 성장과 발전을 거듭해온 것과 다르게 자체적인 투자만으로 이뤄져 더욱 뜻 깊다. 이미 일관제철소 사업 초기부터 기존 인프라를 이용한 브라운필드(Brown Field) 방식이 아니라, 신규 일자리 창출 및 중소기업 육성 등 경제적 파급효과가 큰 그린필드(Green Field) 방식으로 투자하여 경제 활성화에 기여해온 현대제철은 자체 투자만으로 믿기지 않는 성장을 이뤄내 현대차그룹 특유의 불굴의 도전정신과 저력을 국내외에 보여줬다.[7]
현대제철은 2012년까지 3년간 총 81종의 자동차용 열연강판 강종을 개발했다. 이는 현재 국내에서 생산되는 완성차 적용 강판 강종의 대부분인 99%를 대응할 수 있는 수준이다. 고로 가동 원년인 2010년 내판재와 섀시용 강판 전 강종 49종을 개발한 데 이어 2011년에는 외판재 13종과 고강도강 등 22종을 개발했으며, 2012년에는 100~120K급 초고장력강 등 10종을 개발하는 성과를 이뤘다. 2013년에도 자동차용 신강종 개발에 주력하고 있다. 2012년까지 기본 강종 개발에 집중했다면, 2013년 이후 자동차강판 중장기 강종 개발 방향을 신강종·미래강종 개발을 통한 경쟁력 강화로 정하고 차세대 자동차용 신강종을 개발 중이다. 한편 현대제철은 내시효 강판 외에도 내식성을 강화한 섀시용 초고강도 열연도금재와 고강도를 유지하면서도 가공 성형성을 한층 높인 저항복형 50K급 외판 및 사이드아우터용 고강도 외판 등 독자 신강종 개발을 추진하기로 했다.또한 중장기적으로는 고강도를 달성하면서도 성형성을 높인 고망간강, 알루미늄을 첨가해 무게를 대폭 줄인 초고강도 경량강판, 내식성을 높인 아연망간도금강판 등 차세대 신개념 자동차강판 선행 개발에 나선다는 방침이다. 현대제철 당진제철소 완공으로 현대차그룹은 자동차용 강판은 물론 철분말과 특수강까지 아우르는 차세대 자동차용 첨단소재 개발에 본격적으로 돌입해 한 차원 높은 자동차산업 협력 생태계를 구축하게 됐다. 2012년 10월 토목공사에 들어가 2014년 2월 양산을 목표로 건설에 박차를 가하고 있는 현대차의 철분말 공장과 자동차 핵심부품인 엔진 및 변속기의 필수 소재인 차세대 특수강 공급을 위해 2014년부터 본격 추진될 현대제철의 특수강공장 건설을 통해 자동차 부품산업의 경쟁력이 한층 높아질 것으로 기대된다. 현대제철은 당진제철소 내 23만6천㎡ 부지에 1조 원을 투자해 고도화된 정밀압연 설비를 갖춘 특수강공장을 신축하고 제강공정에 고로 쇳물(용선)을 활용해 연산 100만톤 규모의 고청정 특수강 소재를 생산할 계획이다. 현대차가 1천200억원을 투입해 건설 중인 철분말 공장은 또한 연간 2만5천톤의 고품질 철분말 부품소재를 생산함으로써 스웨덴, 미국, 일본 등에서 전량 수입하던 물량을 대체하고 자동차 부품 소재 수급 안정 및 자동차 경량화에 기여할 것으로 전망된다.현대차그룹은 1조1천200억원이 투자되는 특수강과 철분말 등 첨단소재 개발 사업을 통해 국내 부품산업의 글로벌 성장기반을 강화하는 한편 현대·기아차의 품질경쟁력 향상을 실현시킨다는 방침이다.[7] 현대제철은 이번 3고로 화입이 회복세를 보이고 있는 우리나라 경제에 새로운 활력소가 될 것으로 큰 기대를 걸고 있다.우리나라 무역 수지를 개선함으로써 국가 경제 전체에도 긍정적인 영향을 미칠 것으로 기대된다. 현대제철 3고로의 본격적인 가동으로 연간 1천200만톤 규모의 고급 철강재가 국내에 공급되면 연간 8조9천억원 수준의 수입대체 효과가 발생하는 한편, 관련 수요산업의 경쟁력 제고에도 크게 기여할 것으로 예상된다. 우리나라는 1인당 철강소비량 세계 1위, 조강생산량 세계 5위의 철강강국으로 국내 철강업체들은 품질과 가격 측면에서 경쟁력 있는 제품을 생산해 주력 수출산업인 자동차, 조선, 전자, 기계 산업에 공급함으로써 국가 경쟁력 향상에 주축을 담당하고 있다. 그러나 고품질의 쇳물을 생산하는 상공정과 제품을 생산하는 하공정의 불균형으로 연간 2천만 톤이 넘는 소재용 철강재를 일본과 중국 등지로부터 수입하고 있으며 2012년에는 우리나라 조강생산량 6천907만톤의 약 30%에 달하는 2천71만톤의 철강재를 해외에서 수입했다. 그 결과 2012년 대일무역적자 256억 달러 가운데 38억 달러가 철강부문에서 발생했고, 중국산 철강재 무역적자액이 41억 달러를 기록하는 등 심한 무역 불균형을 이루고 있다. 따라서 현대제철 3고로의 본격 가동은 자동차를 비롯한 수요산업의 경쟁력 강화는 물론 무역 역조에 따른 국부 유출을 최소화함으로써 한국 경제에 새로운 활력소가 될 것으로 기대된다.[7]
2020년 12월 22일, 현대제철이 고로에서 배출되는 대기오염물질을 사실상 원천 차단하는 기술을 세계 최초로 개발해 실제 공정에 성공적으로 적용했다. 현대제철은 고로 정기보수 후 고열의 바람을 다시 불어넣는 재송풍 작업 시 가스 청정 밸브인 1차 안전밸브를 통해 고로 내부에 남아있는 유해가스를 정화 후 배출하는데 성공했다. 2020년 상반기 진행한 고로 정비에 앞서 고열의 공기 주입을 멈추는 작업인 휴풍에 이어 재송풍 과정에서도 가스 청정 밸브가 성공적으로 작동해 기존 고로 브리더보다 배출 가스 불투명도가 현저히 개선되는 결과를 얻었다. 이로써 현대제철은 환경단체에서 지적해온 고로 대기오염물질 배출 문제를 해결하며, 제철소 건설 때부터 지향해온 친환경 제철소로서의 명성을 다시 한 번 증명하게 됐다. 현대제철에 따르면 2020년 11월 3일, 2고로를 시작으로 24일 1고로 재송풍때 가스 청정 밸브를 활용해 대기오염물질을 저감시키는데 성공했다. 또한 2020년 12월 10일에는 환경부에서 당진제철소를 방문해 3고로 재송풍 시 가스 청정 밸브의 정상가동 상황을 직접 점검하고, 배출가스의 불투명도를 측정해 긍정적인 결과를 확인했다. 현대제철은 2019년 3월 고로 브리더의 대기오염물질 배출 논란이 발생하자 즉시 유럽의 전문 엔지니어링 기술회사와 긴밀하게 협업하였고, 3개월여의 기술검토 끝에 세계 최초로 고로 브리더의 대기오염물질 배출을 획기적으로 줄이는 가스 청정 밸브를 성공적으로 개발했다. 이후 유럽 특허 출원까지 마쳤으며, 이를 1차 안전밸브라고 명명했다. 현대제철은 직경 1.5m, 길이 223m의 파이프로 이뤄진 1차 안전밸브를 2020년 1월 3고로에 먼저 설치해 휴풍 시 성공적인 테스트 결과를 얻었고, 상반기 모든 고로에 완벽히 설치했다. 당진제철소 관계자에 따르면 현대제철의 1차 안전밸브는 조업 안정성까지 확보한 환경·안전설비인 만큼, 국내외 제철소에서 설치를 원할 경우 적극적으로 기술을 지원할 계획이다. 현대제철은 고로 잔류가스를 정화해 배출하는 설비 및 솔루션을 세계 최초로 개발해 적용한 만큼 향후 모든 제철소의 고로 브리더와 관련한 대기오염물질 배출 논란을 불식시킬 수 있을 것으로 평가되고 있다. 한편 현대제철은 2019년 10월 당진시와 제철소 온실가스 저감 및 환경개선을 위해 상호협력을 다짐하는 협약을 체결하고 2021년부터 5년간 제철소 온실가스 저감 및 환경개선에 4,900억 원의 추가 투자를 결정했다. 특히 2025년까지 코크스 건식소화설비(CDQ)를 설치함으로써 코크스 냉각 시 발생하는 폐열을 회수해 이를 증기 및 전력으로 재생산하는 방식을 활용하여 50만 톤의 온실가스를 감축할 수 있을 것으로 예상하고 있다. 2016년부터 2021년까지 환경에 투자한 5,100억원을 포함하면 현대제철의 10년간 환경 관련 투자액은 총 1조 원에 육박한다.[8]
전기로사업
현대제철은 철스크랩을 원료로 쇳물을 만들어 내는 전기로 분야에서 국내 최대 생산능력과 최고의 기술력을 보유하고 있다. 인천, 포항, 당진의 전기로 공장을 통해 연산 1,200만 톤의 생산능력을 갖춘 현대제철은 60여 년 동안 축적된 전기로 기술력을 토대로 국내 철강 업체 가운데 가장 많은 세계일류상품을 보유하고 하고 있으며 지속적인 연구개발 및 투자를 통해 다양한 철강재 수요에 능동적으로 대처하고 있다.[2]
2007년 6월 11일, 현대제철은 당진공장 A열연공장에서 신규 연주설비를 준공하고 국내 최초로 철스크랩을 원료로 쇳물을 만드는 전기로제강 방식을 통해 210mm 두께의 자동차강판 소재용 슬래브 생산에 성공했다. 이는 세계적으로도 동경제철에 이어 두 번째로 이룬 성과이며 특히 신규 연주설비의 설치를 시작한지 불과 6개월만에 공사를 마무리 짓고 정상 가동시킴으로써 세계 최고 수준의 제강 및 연주 기술력을 인정받게 되었다. 이에 앞서 현대제철은 몇 십년간 축적된 제강기술을 기반으로 2004년 10월 당시 한보철강을 인수한 이후 불과 7개월만에 55mm 두께의 박슬래브를 소재로 열연강판을 생산하는 A열연공장의 운영을 완전 정상화시킴으로써 우수한 기술력을 증명했다. 210mm 슬래브 생산 성공으로 고로 완공시 필요한 제강 및 연주기술의 토대를 이미 상당부분 확보한 것으로 평가받았다. 또한 현대제철은 쇳물에서부터 최종제품인 열연강판까지 생산하는 일관제철공정 쇳물을 2010년 1기 고로 완공 이전에 앞당겨 실현하게 되면서 쇳물 생산 이후의 공정, 즉 제강ㆍ연주ㆍ압연공정의 조기 기술 확보 및 조업기술 향상에 박차를 가했다. 장치산업인 일관제철소의 특성상 생산과 품질이 일정 수준에 도달하기 위해서는 수년간의 연구개발기간이 필요하다. 따라서 현대제철은 신규 연주기의 가동을 통해 조기에 210mm 두께의 슬래브 조업기술 확보가 가능할 뿐만 아니라 B열연공장에서의 압연기술 또한 축적이 가능할 전망이다. 현대제철은 고로 1호기가 본격적인 조업에 돌입하는 2010년까지 신규 연주설비에서 다양한 강종의 슬래브를 생산하는 한편 B열연공장에서 다양한 강종에 맞는 가열온도와 압연압력, 압연속도 등 데이터를 축적할 계획이다. 또한 2007년부터 생산을 통해 2년여를 축적하게 되는 조업기술을 고로가 본격적으로 가동하는 2010년 이후 일관제철공정에 바로 적용함으로써 일관제철소 조기정상화 및 생산제품의 품질안정화에 크게 기여할 것으로 기대하고 있다.특히 현대제철을 포함해 현대하이스코와 현대기아차 연구인력들이 연구개발을 진행 중인 철강연구소와 함께 제강, 연주 및 압연기술의 선행 연구를 수행함으로써 기존 제철소들보다 안정화기간을 획기적으로 단축시킬 수 있을 것으로 기대된다. 이와 함께 현대제철 당진공장은 최근 열연강판에 대해 일본의 새로운 공업규격인 新 JIS 규격을 획득해 생산제품에 대한 품질의 우수성도 함께 입증, 해외 수출에서도 유리한 고지를 선점하게 됐다. 新 JIS 규격은 지난 2005년 새롭게 규정된 일본공업규격으로 기존의 제품인증 위주에서 품질경영체제인 ISO를 통합한 개념으로 확대한 공업규격으로 2008년 10월 이후에는 모든 JIS 규격을 新 JIS 규격으로 전환해야 한다.현대제철은 향후 다양한 해외 규격 인증 획득을 추진함으로써 제품의 우수성을 입증하고 해외 시장 확대에도 총력을 기울여나갈 계획이다 라고 밝혔다.[9]
2008년 9월 30일, 현대제철이 전기로제강업체로는 세계 최초로 빔블랭크(Beam Blank)1를 이용하여 400규격의 극후 H형강을 개발하는데 성공했다. 400규격 극후 H형강은 그동안 고로업체가 슬래브(Slab)2를 반제품으로 이용해 제조했던 제품으로 주로 고층건축용 기둥재로 사용되며 전량 일본에서 수입되어 왔다. 현대제철은 "인천 대형압연공장에서 그동안 축적되어 온 제어압연기술로 빔블랭크를 이용해 고로업체의 전유물로 인식되어 온 400규격 극후 H형강(H458×417×30/50, 415kg/m) 개발에 성공했다"며 "이로서 연간 2만여톤 수준의 국내 수요가 있는 이 제품의 전량 수입대체가 가능하게 됐다."고 밝혔다. 또한 "이번 극후 H형강 개발로 국내 동종업체와의 기술력 차이를 확실히 입증하는 한편 해외 고로업체들과의 경쟁에서도 어깨를 나란히 할 수 있는 계기를 마련하게 되었다."고 덧붙였다. 현대제철은 400규격 극후 H형강의 개발로 연간 330억원 수준의 수입대체 효과와 내수제품 다양화에 따른 신수요 창출을 기대하고 있으며 향후 지속적으로 고객들의 요구에 부응하는 제품 개발에 모든 역량을 집중해 나간다는 계획이다. 한편 현대제철은 이에 앞서, 지난 2007년 11월 극후 고강도 H형강인 'H305×305×26.8/44.1'의 국산화에 성공한 바 있는데 이 제품은 빔블랭크를 반제품으로 사용해 제품을 생산하는 것으로 해외 전기로업체에서도 생산이 가능한 제품이었다. 하지만 현대제철은 극후 H형강의 국산화에 성공한지 불과 10개월여 만에 빔블랭크를 소재로 고로업체들만 생산해온 400규격의 극후 H형강까지 개발하는데 성공함으로써 그 기술력을 인정받았다. 극후 H형강은 플랜지(flange) 두께가 40mm 이상인 H형강을 지칭하며 초고층 빌딩의 설계기술 진전과 함께 가공의 합리화, 검사의 간소화 등을 통한 건설비용 절감의 필요성이 대두되면서 각광을 받고 있다. 범용 H형강의 플랜드 두께가 10~20mm 수준이라는 것을 감안할 때 플랜지 두께가 상당히 두꺼운 제품이다.[10]
2020년 4월 27일, 현대제철은 인천공장 120톤 전기로에‘원료 운영 최적화 시스템’을 구축했다고 밝혔다. 이로써 일관제철소 고로에 이어 전기로 부문에서도 빅데이터 기반의 원료 운영 최적화 시스템이 도입됐다. 제철소에서 시작한 스마트엔터프라이즈 혁신이 전기로 부문까지 본격 확대됐다는 데 의미가 있다. 현대제철은 5개월간 데이터 축적 및 분석을 실시했으며 약 6억6000만원의 예산을 투입해 인프라를 갖췄다. 또한 파일럿 테스트를 통해 원료 투입 및 조업 개선점을 확인했다. 현대제철이 구축한 전기로 원료 운영 최적화 시스템의 핵심은 원료창고의 전자맵이다. 전자맵으로 실제 원료창고를 똑같이 구현해 철스크랩의 중량, 등급 및 위치가 한눈에 파악될 수 있도록 했다. 기존에는 등급별 철스크랩의 일부 혼적 보관이 불가피했다. 또한 작업자는 주문서에 따라 철스크랩을 육안으로 확인해 전기로에 투입했다. 이로 인해 실제 투입하는 철스크랩의 등급과 양을 정확하게 파악할 수 없어 제품 품질 및 조업 영향 분석, 원가 계산이 어려웠다. 현대제철은 이를 해결하기 위해 우선 원료창고 내부에 가벽을 세워 철스크랩을 등급별로 세분화해 적재하고 이를 전자맵으로 구현했다. 또한 레이저센서를 설치해 철스크랩을 운반하는 크레인의 위치가 전자맵에 실시간 표시되도록 했다. 따라서 작업자는 실시간으로 어느 장소에 어떤 등급의 철스크랩이 적재되고 이송되는지 한눈에 파악이 가능해졌다. 또한 원료창고에서 이송·보관·투입되는 모든 철스크랩의 등급과 정보는 전자맵에 자동으로 입력되어 데이터로 축적된다. 이는 향후 품질 최적화 및 조업 개선을 위한 기초자료로 활용 된다. 현대제철 관계자는 “철스크랩에 대한 정확한 데이터가 집계되면 품질별 소요량 예측과 조업 분석이 가능해 제품 생산 전 공정에 파급 효과가 크다”며 “단기적으로 불필요한 철스크랩의 투입량을 줄일 수 있을 뿐 아니라 향후 제품 품질 예측이 가능해져 전반적인 조업 효율성을 개선할 수 있다”고 말했다. 현대제철은 120톤 전기로를 시작으로 올 하반기부터는 전 사업장의 전기로에 시스템 구축을 검토하고 있다. 현대제철은 인천, 포항 당진에 총 11기의 전기로를 보유하고 있으며 투자가 완료되면 전기로 부문의 조업 효율성 향상, 품질 개선, 원재료 구매 비용 절감 등의 효과가 기대된다. 회사 측은 총 70억 원 이상의 개선 효과가 있을 것으로 내다봤다. 한편 현대제철은 2017년부터 스마트 엔터프라이즈를 구축하기 위한 혁신에 속도를 내고 있다. 그 일환으로 올해 초에는 프로세스 혁신 조직을 사장 직속으로 전환해 시스템, 인프라 부문의 스마트 매니지먼트 구축에 힘을 쏟고 있다. 현대제철은 향후 2025년까지 제조, 생산 부문의 스마트 팩토리 구축과 관리 부문의 스마트 매니지먼트 융합을 통해 최적의 의사결정 시스템을 만들어 스마트엔터프라이즈 혁신을 완성할 방침이다. 안동일 현대제철 사장은 “스마트 엔터프라이즈의 핵심은 고객 가치 극대화”라며 “전사적인 데이터 융합을 통해 고객 중심으로 모든 프로세스를 운영하고 이러한 시스템과 문화를 정착시켜 최적화된 의사결정 시스템을 구축할 때 현대제철의 지속성장이 가능할 것”이라고 말했다.[11]
AP(Automotive Part)/강관사업
현대제철은 더욱 가볍고 안전한 자동차를 만들기 위해 TWB(Tailor Welded Blanks), 하이드로포밍(Hydroforming), 핫스탬핑(Hot Stamping)등의 공법을 적용한 자동차부품 소재 개발에 힘쓰고 있다. 현대제철의 자동차 부품에는 ‘연비절감을 위한 차제 경량화’·‘안전성을 고려한 내충격성 강화’·‘원재료 사용성’ 향상을고려한 첨단 자동차 경량화 공법으로, 이는 자동차의 연비를 향상시켜 지구 온난화의 주범인 자동차의 배기가스를 줄이며 동시에 안전도까지 향상시키는 제품으로 생산되고 있다.[2]
2015년 4월 8일, 현대제철이 계열사인 현대하이스코를 완전 합병하기로 했다. 현대제철은 2013년 이미 현대하이스코의 냉연강판 부문을 흡수한 바 있다. 이번에 강관(파이프) 사업과 해외 냉연강판 가공 사업장을 추가 인수함으로써 자산 31조원 규모의 ‘자동차 소재 전문 제철소’로 거듭나게 됐다. 현대제철은 2015년 4월 8일 이사회를 열어 현대하이스코 합병안을 결의했다고 밝혔다. 두 업체는 2015년 5월28일 주주총회 승인을 거쳐 7월1일까지 합병을 마무리하기로 했다. 현대제철이 신주를 발행해 현대하이스코 주식 1주당 현대제철 주식 0.8577주를 하이스코 주주에게 교부하는 방식으로 이뤄진다. 현대제철은 2014년 기준으로 자산 28조9000억원, 매출액 16조8000억원을 기록했다. 현대하이스코는 자산 2조5000억원, 매출액 4조2000억원이다. 합병 결의에 따라 자산규모 31조원, 매출 20조원, 조강능력 세계 14위의 대형 철강업체가 탄생하게 됐다. 현대차그룹은 자동차용 강판을 현대제철과 현대하이스코 두 업체로부터 공급받아왔다. 현대제철은 용광로에서 쇳물로 열연강판을 만든다. 이 제품을 현대하이스코가 구매해 자동차에 필요한 냉연강판을 만들어 현대차나 기아차에 납품하는 형태다. 2013년 12월 현대제철이 현대하이스코 매출의 60%가량을 차지하던 냉연부문을 인수함으로써 사실상 현대제철은 독자적으로 현대·기아차에 강판을 납품할 수 있는 체제를 갖췄다. 현대하이스코가 운영하던 강관사업과 냉연강판을 가공하는 해외 스틸서비스센터(SSC)를 인수하게 됨으로써 명실상부한 자동차용 철강재 소재 기업이 된 것이다. 업계에서는 이번 합병으로 현대제철의 해외 영업력이 높아질 것으로 내다봤다. 현대제철은 중국 칭다오에만 해외 생산공장을 운영하고 있다. 그러나 현대하이스코는 현대·기아차 해외공장 인근에 자동차 강판을 가공하는 SSC 13개를 9개국에서 운영하고 있어 시너지 효과가 나타날 것으로 기대하고 있다. 강관사업 부문을 추가한 것도 장기적으로 현대제철 수익성을 높이는 데 도움이 될 것이라는 분석이 많다. 2015년 들어서 셰일가스 사업 부진으로 어려움을 겪는 강관사업을 현대제철이란 덩치 큰 업체가 맡게 됨으로써 새 시장 개척 등을 할 수 있는 계기가 마련된 것이다. 현대제철이 현대하이스코를 완전 합병한다는 소식이 전해지면서 이날 두 업체 주가는 각각 6.06%, 8.16% 올랐다.[12]
현대제철이 돈 되는 강관사업 영역을 넓히고 있다. 2018년 18일 철강업계에 따르면 현대제철은 최근 울산의 강관 제조·판매업체인 현대알비에서 6만2천t 규모의 후육관 생산공장을 인수했다. 후육관(초대형 파이프)은 송유관과 시추관, 대형 건축물 등에 쓰이는 강관이다. 업계는 미국 보호무역주의와 후판을 주로 사가는 조선업계가 불황에 빠지는 이중고를 타개할 돌파구로 강관 사업다각화 카드를 꺼내든 것으로 분석하고 있다. 후육관은 두께가 20~140㎜인 파이프로 두께 6㎜ 이상인 후판을 두드려 만든 철강재다. 주로 해양플랜트 구조물, 송유관, 발전소 열배관재, 내진건축용으로 쓰인다. 국내에는 스틸플라워가 이 업종의 선두주자로 꼽히고 있다. 현대제철은 이번 강관공장 인수로 약 20년만에 후육관 사업에 다시 뛰어들었다. 현대제철은 미국 정부가 유정용강관 등 한국산 강관에 대한 보호무역주의 기조 강화가 이어지자 후육관을 통한 사업다각화로 활로를 모색하고 있다.[13]
2020년 1월 3일, 현대제철이 강관사업부를 자회사인 현대BNG스틸에 매각하는 방안을 검토하고 있다. 철강업계에 따르면 현대제철은 강관사업부를 매각하기 위해 외부 컨설팅을 했으며 매수 주체인 현대BNG스틸에 대한 컨설팅도 하고 있다. 업계에서는 이르면 이달에 매각 절차가 진행될 수도 있을 것으로 보고 있다. 현대제철은 자동차·조선·건설 등에 사용하는 열연·냉연·후판·강관 제품을 생산하고 있다. 이 중 강관사업부를 현대BNG스틸에 넘기며 사업 포트폴리오를 재정비하는 것이다. 강관사업부는 2015년 현대제철이 현대하이스코를 인수·합병(M&A)하면서 현대하이스코의 강관사업부를 흡수했다. 현대하이스코 강관 영업부서는 현대제철 영업본부로, 강관 생산부서는 현대제철 울산공장으로 편입됐다. 매각 작업이 실제 이뤄지면 강관사업부가 현대제철에 편입된 지 5년 만에 다시 분리되는 것이다. 현대제철은 2019년 미·중 무역분쟁과 전방산업인 조선·자동차·건설산업 침체 영향으로 실적 부진이 이어지며 어려운 시기를 보냈다. 철강 제품 판매량이 감소한 데다 평균 판매단가도 하락했기 때문이다. 2019년 3분기 영업이익은 전년도 같은 기간보다 67%가량 줄었고, 4분기에는 적자를 기록할 전망이다. 이 같은 상황에서 현대제철은 강관사업부를 현대BNG스틸에 이관해 모든 역량을 자동차 소재 전문 제철소로 거듭나는 데 집중할 것으로 보인다. 부진한 실적을 개선하기 위한 일종의 사업 포트폴리오 재편으로 볼 수 있다. 강관사업부는 설비 가동률이 다른 사업부에 비해 낮은 데다 생산 실적 역시 매년 감소하는 추세다. 현대제철이 2019년 발표한 사업보고서에 따르면 3분기까지 강관 등 생산설비 가동률은 63.3%에 머물렀다. 냉연(108.8%), 후판(99.2%), 열연(89.1%), 봉형강(86.7%) 등에 비해 현저히 낮은 수준이다. 생산 실적도 2017년 163만8000t에서 2018년 162만4000t으로 줄었고 2019년 3분기에는 107만1000t에 그쳤다. 매수 주체로 검토되는 현대BNG스틸은 스테인리스 냉연강판을 생산하는 제조업체로 스테인리스 강판 비중이 전체 매출액 중 약 97%를 차지하고 있다. 현대제철 지분율은 41.12%다. 고(故) 정주영 현대그룹 회장 손자인 정일선 사장이 경영을 맡고 있다.[14]
2020년 3월, 현대제철이 미래 성장 동력 확보를 위해 고부가가치 제품군인 글로벌 프리미엄 제품의 판매 확대와 경쟁력 강화에 집중한다. 현대제철은 글로벌 프리미엄 제품 중에서도 자동차용 고부가 강판과 AP(Automotive Parts) 소재 등에 전사적인 역량을 집중하고 있다. 특히 자동차 소재의 경쟁력 강화를 위해 미래 수요에 선제적으로 대응하고 글로벌 유수 완성차 메이커의 공급을 지속적으로 확대함으로써 자동차 소재 전문 제철소로서의 위상을 더욱 높인다는 방침이다. 현대제철은 특히 자동차 소재 가공사업 분야인 AP(Automotive Parts)에 투자를 강화하고 있다. 현대제철은 지난 2009년 고강도 차량 부품 소재를 만들 수 있는 핫 스탬핑(Hot Stamping)에 대한 연구를 본격화했으며, 2009년 사업화를 시작했다. 핫스탬핑이란 950°C의 고온으로 가열된 철강소재를 금형에 넣고 프레스로 성형한 뒤, 금형 내에서 급속 냉각시키는 공법이다. 이를 통해 가볍고 인장강도가 높은 초고장력강을 만들 수 있다. 핫스탬핑 공법을 적용하면 고강도에서도 성형성을 확보할 수 있고 알루미늄이나 마그네슘 등의 경량화 소재 대비 비용을 크게 절감할 수 있다는 장점이 있다. 자동차 산업의 트렌드가 안정성을 바탕으로 한 경량화 등에 맞춰지면서 현대제철이 선제적으로 연구개발 한 핫스탬핑 분야도 최근 본격적으로 확장되기 시작했다. 이에 따라 현대제철은 지난 2015년 자동차 가공사업 부문을 예산공장으로 통합해 본격적으로 운영하고 있다. 또한, 현대제철의 AP 사업은 기술 및 가격 경쟁력에서 세계 최고 수준으로 평가받고 있어 글로벌 시장에서의 성장이 한층 기대된다. 이와 관련해 2021년 1월 양산을 목표로 체코에 핫스탬핑 공장을 신설하고 있어 유럽 등 글로벌 시장 공략에 박차를 가할 수 있을 것으로 전망된다. 현대제철이 580억 원을 투자해 추진하고 있는 체코 핫스탬핑 공장은 체코의 공업도시인 오스트라바시(市)에 건설되고 있으며 2021년 1월 양산을 목표로 하고 있다. 핫스탬핑 설비 2기, 블랭킹 설비(정해진 형상으로 코일을 절단하는 설비) 1기를 갖춰 연간 335만 매의 자동차용 소재를 공급할 수 있다. 현대제철은 체코 핫스탬핑 공장을 통해 유럽 현지 수요 물량에 대해 더욱 신속하게 대응하는 한편, 글로벌 자동차강판 수주 확대에도 보탬이 될 수 있을 것으로 기대하고 있다.
또한, 지난 2019년 4월 론칭한 자동차 전문 솔루션 브랜드 H-SOLUTION은 자동차 소재 분야에 대한 현대제철의 경쟁력을 한층 높여줄 것으로 기대되고 있다. H-SOLUTION은 고장력강·핫스탬핑 등 자동차용 소재 단위에서부터 성능과 원가, 품질을 향상할 수 있는 물성·성형·용접·방청·도장·부품화를 아우르는 서비스를 나타내는 브랜드다. 2020년 들어서는 H-SOLUTION 전용 홈페이지와 앱을 개설해 현대제철만의 다양한 응용 기술 정보와 서비스를 제공하고 있다. 현대제철은 2020년 1월 회사 홈페이지 내에 AE서비스 포털을 오픈했다. AE는 ‘Application Engineering’의 약자로 고객사의 경쟁력을 극대화하기 위해 기획·설계 단계부터 생산·판매에 이르는 모든 프로세스에서 차별화된 가치를 만들어 제공한다는 현대제철만의 사업 전략을 뜻한다. 이번 홈페이지 구축으로 고객들은 2019년 4월 현대제철이 출시한 자동차 솔루션 전문 브랜드인 H-SOLUTION을 중심으로 회사가 생산하는 자동차 강재 제품 및 부품적용에 필요한 응용 기술 등을 한 눈에 돌아 볼 수 있게 됐다. 동일한 내용을 적용한 모바일 앱도 개발, 스마트폰으로 언제 어디서나 확인할 수 있게 편리함을 더 했다. 이외에도, 현대제철이 2019년 11월 출시한 고강도 내마모강 브랜드 WEAREX(웨어렉스)는 자동차 소재 분야 현대제철의 한층 높아진 기술 경쟁력을 보여주는 사례다. WEAREX는 WEAR+Resistant+EXcellent 단어를 조합해 외력에도 닳지 않는 철이라는 의미를 가진 현대제철 내마모강 판재 브랜드명으로 기존 제품 대비 경도 및 가공성이 크게 향상된 것이 장점이다.고도의 열처리 제어 및 최적 비율의 탄소, 보론, 크로뮴 등 합금원소 첨가로 경도 및 내마모성이 매우 우수하고 제강공정에서부터의 엄격한 성분 관리로 고청정성을 갖춘 제품이다. 부품의 성능을 극대화하고 기계 수명을 오래 유지할 수 있어 자동차의 엔진, 트렌스미션 등 반복 하중이 발생하는 구동계 부품에 최적의 효과를 낼 수 있을 것으로 기대되고 있다. 현대제철은 WEAREX 브랜드를 바탕으로 열연용 내마모강 판매량을 연간 5만 톤 수준에서 13만 톤까지 신장시킬 계획이다. 또한, 글로벌 자동차 공급 확대하기 위한 소재 및 부품 개발과 특화된 브랜드화를 통한 고객 마케팅을 강화하고 고성능 신제품 개발을 가속함으로써 올해 글로벌 프리미엄 제품 판매 911만 톤, 글로벌 자동차강판 판매 100만 톤을 달성한다는 방침이다. 한편 현대제철은 국내 최초 철강사로서 지난 67년간 수많은 위기를 극복하며 성장해온 저력을 근간으로, 기본에 충실하면서도 업계의 변화를 주도해 나갈 방침이다. 이를 위해 올해 집중 전략 방향을 기본에 충실한 성장, 사업구조 최적화, 선제적 변화 대응, 사회적인 책임 실천 등 4가지로 선정했다. 현대제철은 본원적 경쟁력에 방점을 두고 지속 가능한 성장 잠재력을 확보해 불확실한 경영환경에 대응하겠다는 포부를 드러냈다.[15]
현대제철이 올해 저(低)수익사업에 대한 재편 작업을 이어간다. 현대제철은 지난해 대표적인 적자사업으로 지목돼왔던 단조사업부문 분사를 시작으로 열연 전기로 폐쇄, 컬러강판 사업 중단 등 굵직한 구조개편을 단행했다. 하지만 여전히 중국법인, 강관부문, 스테인리스(STS)부문 등 조정을 검토 중인 사업들이 남아 있어 올해는 해당사업을 중심으로 추가 재편이 이뤄질 전망이다.현대제철은 28일 가진 연간 실적 컨퍼런스콜에서 "지난해 단행했던 사업 구조조정 효과는 올해부터 본격화될 것으로 기대된다"면서 "올해도 핵심사업을 제외한 전 부문에서 지속적으로 이익이 어렵다고 판단되는 사업에 대해 조정을 해나갈 계획이다"고 밝혔다. 올해 현대제철 사업재편 대상으로 유력하게 물망에 오르고 있는 부문은 중국법인, 스테인리스사업과 강관사업 등이다.현대제철 강관부문 재편 역시 눈여겨볼 필요가 있다. 현대제철 강관은 지난 2015년 현대하이스코를 흡수합병하면서 편입한 사업이다. 현대제철은 타 사업과의 시너지가 적고 상대적으로 다른 품목대비 수익성이 저조한 강관사업부를 매각하거나 별도의 법인으로 분리하는 방안을 검토해왔다. 관련업계에서는 지난해 구체적인 움직임이 있을 것으로 예측했지만 '코로나19' 바이러스 확산 등 복합적인 요인들이 겹치며 재편에 어려움을 겪고 있는 것으로 알려졌다.한편 현대제철은 과거 대규모 고로 투자와 기업 인수합병 등을 통해 꾸준히 몸집을 키워왔으나 최근 몇 년간 자동차, 건설, 조선 등 전방 수요산업 위축과 '코로나19' 바이러스 여파까지 겹치면서 위기에 봉착했다. 현대제철은 이를 만회하기 위해 모든 사업을 원점에서부터 면밀히 재검토하고 가장 효율적인 조직을 만드는데 초점을 맞추고 있다.[16]
제품소개
제품군
열연
최신 설비를 통한 고품질 열연 생산한다. 열연은 반제품인 슬래브를 가열해 압연 후 코일 형태로 감은 열연강판을 말한다. 현대제철은 연간 980만톤의 열연 생산능력을 보유하고 있으며, 일관제철 생산체제와 최신 설비로 고품ㅈ질의 열연제품을 생산하고 있다. 열연은 자동차용, 구조용, 강관용 등 산업전반의 다양한 분야에 널리 사용되고 있다.[2]
- 자동차용 : 자동차의 수명은 물론 안전성과 직결되므로 우수한 강도 및 내피로성을 보유하고 있으며, 점차 다양해지는 차량 디자인에 맞춰 쉽게 변형 가능한 고가공성과 차체 경량화에도 적합한 성질을 가지고 있다. 주로 자동차의 차체를 이루는 프레임, 휠, 외판 등에 사용되고 있다. 주요제품은 SPCC/D-E, PCC/D-E, SPRC340E-E, SPFC340BH-E, SGARC340E/BH-E, SAPH340/370/400/440, SPFH540/590/780, HS540/590/780AS 등이 있다.
- 구조용 : 구조물의 뼈대 역할을 하기 때문에 기계적 성질이 매우 중요하며, 각 용도에 필요한 항복강도, 인장강도, 연신율, 굽힘성, 충격인성 등을 보유하고 있다. 일반구조용과 용접구조용으로 구분되며 주로 교량ㆍ선박ㆍ차량 등의 구조물에 사용되고 있다. 주요제품은 SPHC, SS400/490/540/590, SM490A/B/YA/YB, A36, A1011, A572, EN-S235/275/325/355JR 등이 있다.
- 강관용 : 제강 및 열간압연 과정에서 화학성분과 압연온도를 조정해 최적의 기계적 성질과 용접성능을 구현해 우수한 용접성과 성형성을 보유하고 있다.일반용, 기계구조용, 열교환기용, 내지진용, 송유관ㆍ유정관용 등으로 구분되며 주로 일반 강관, 전선관, 보일러 등에 사용되고 있다. 주요제품은 SPHT1/2/3, STKSTB340/410/510, SN400B/490B, HPCD290/340/410/440/470/510A, API 5L/5CT 등이 있다.
- 고압가스용기용 : 열간압연 과정에서 공정별 온도를 관리해 우수한 가공성 및 길이별 재질편차를 최소화했ㄷ다. 특히, 안전성과 직결되므로 불순물 관리를 통해 우수한 청정도를 유지하고 있다. 주로 압력용기, 가스탱크 등에 사용되고 있다. 주요제품은 SG255/295/325/365 이다.
- 고탄ㆍ합금강 : 반복적인 작업 및 마찰에 대한 내성이 요구되므로 다량의 탄소 및 합금원소를 첨가해 고강도, 고경도, 내마모성을 보유하고 있다. 주로 자동차용 부품, 체인, 칼날, 공구 등의 특수용도에 사용되고 있다. 주요제품은 S45/50/55C, SCM415/435, SNCM220, SK85, 51CrV4 등이 있다.
냉연
냉연은 열연을 상온에서 압연한 강판으로 철강제품 중에서 가장 생산하기가 어렵고, 높은 기술력을 필요로 하기 때문에 '철강제품의 꽃'이라고도 불린다. 냉연강판은 두께가 얇고 표면이 미려해 우리 생활과 밀접한 자동차, 가전제품, 건축자재 등의 외판과 내장재로 사용된다. 현대제철은 연간 700만톤의 냉연강판 생산능력을 가지고 있으며 최근에는 세계적인 자동차 경량화 트렌드에 발맞춰 초고장력 강판과 같은 고부가가치 냉연강판 개발에 매진하고 있다.[2]
- 산세도유강판 : 열연강판의 표면에 부착된 산화철과 불순물을 염산 등으로 제거한 후 산화방지를 위해 강판 표면에 오일(Oil) 처리한제품이다. 주로 자동차, 건재, 파이프용 소재 등으로 사용되고 있다. 주요제품은 SPHE, SPHD, SPHC, SAPH310, SAPH370, SAPH400, SAPH440, SPFH540, SPFH590, JIS-SPHC, JIS-SPHD, JIS-SPHE, ASTM A1011, EN DD11, DD12 등이 있다.
- 열연도금강판 : 열연강판 표면에 아연도금을 처리한 제품으로 우수한 내식성을 보유하고 있다. 부식에 강하기 때문에 펜스, 컨테이너, 가드레일, 농업용 파이프 등 건축 및 산업용 자재로 사용되고 있다. 주요제품은 SGHC, SGH340, SGH370, SGH400, SGH440, SGH490, JIS-SGHC, JIS-SGH340, JIS-SGH400, JIS-SGH440, JIS-SGH490 등이 있다.
- 전기아연도금강판 : 냉연강판 또는 열연강판 표면에 아연을 전기도금한 제품으로 우수한 내식성과 가공성을 보유하고 있다. 주로 TV, 냉장고, 세탁기 등의 가전제품 소재로 사용됩니다. 주요제품은 SECC, SECD, SECE, SECEN, SEFC340, SEFC390, SECUD, JIS-SECC, JIS-SECD, JIS-SECEN, EN DC01+ZE, EN DC03+ZE, EN DC04+ZE 등이 있다.
- 융융아연도금강판 : 용융아연도금강판은 냉간압연된 강판의 표면을 용융아연도금한 제품으로 내식성이 우수하며 주로 가전용 및 건자재, 자동차의 내부 부품에 사용되고 있다. 합금화용융아연도금강판은 냉간압연된 강판의 아연도금을 합금화 처리한 강판으로 용접성 및 가공성이 우수하며 주로 자동차의 내ㆍ외판용으로 사용되고 있다. 주요제품은 SGCC, SGCD, SGCD1, SGCD2, SGCD3, SGC340, SGC370, SGC400, SGC440, SGC570, JIS-SGCC, JIS-SGCD, ASTM A653, EN DX51D+Z, EN DX52D+Z, EN DX54D+Z, SGACC, SGACD, SGACEN, SGACUD, SGARC340, SGARC440, SGAFC590 등이 있다.
- 컬러강판 : 용융아연도금강판은 냉간압연된 강판의 표면을 용융아연도금한 제품으로 내식성이 우수하며 주로 가전용 및 건자재, 자동차의 내부 부품에 사용되고 있다. 합금화용융아연도금강판은 냉간압연된 강판의 아연도금을 합금화 처리한 강판으로 용접성 및 가공성이 우수하며 주로 자동차의 내ㆍ외판용으로 사용되고 있다. 주요제품은 SGCC, SGCD, SGCD1, SGCD2, SGCD3, SGC340, SGC370, SGC400, SGC440, SGC570, JIS-SGCC, JIS-SGCD, ASTM A653, EN DX51D+Z, EN DX52D+Z, EN DX54D+Z, SGACC, SGACD, SGACEN, SGACUD, SGARC340, SGARC440, SGAFC590 등이 있다.
후판
후판은 일반적으로 두께 6mm 이상의 두꺼운 강판으로, 반제품 슬래브를 열간압연한 후 냉각과 열처리 등의 후속 공정을 통해 만들어진다. 후판은 재질에 따라 일반구조용, 용접용, 보일러용, 대(구)경 강관용 등으로 규격이 정해진다. 용도별로는 조선용, 해양구조용, 용접구조용, 송유관용, 압력용기용, 교량용 등으로 구분할 수 있다. 현대제철 당진제철소에서는 연간 350만 톤의 후판을 생산할 수 있으며 열처리 QT 설비 등 최신 설비를 갖추고 있다. 또한 국내 최초로 러시아, 프랑스 등으로 부터 극저온 고성능 후판에 대한 선급인증을 받는 등 세계적으로 제품의 우수성을 인정받고 있다.[2]
- 조선용 : 각국 선급협회로부터 제조법 승인을 받아 선급 일반용과 고장력강을 생산하고 있다. 최근 선박 경량화에 따른 품질의고급화 및 다양화 등 고객 요구에 대응하기 위해 고강도화, 저온인성, 대입열 용접 특성을 보유하고 있다. 주로 탱커,벌커선, 컨테이너선, LNG선 등의 격벽, 상부 갑판, 해치 덮개 등에 사용되고 있다. 주요제품은 A, B, D, E, AH/DH/EH 32, 36, AH/DH/EH/FH 32, 36-TM 등이 있다.
- 압력용기용 : 압력용기용 후판은 고압의 환경에서 사용되는 경우가 많으므로 우수한 내열성, 내식성을 보유하고 있다. 사용온도에 따라 용도가 구분되므로 고온용·중상온용·극저온용으로 제작되며 주로 가스탱크, 원유 저장용기, 보일러, 열교환기, 발전설비 등에 사용되고 있다. 주요제품은 A203, A285, A353, A387, A516, A515, A537-CL1/2 등이 있다.
- 일반ㆍ용접구조용 : 일반/용접구조용 후판은 건축구조물이 대형화되고 초고층화됨에 따라 사용이 확대되고 있다. 주로 교량, 산업기계, 건축, 해양구조물 등에 사용됩니다. 주요제품은 40KG급, 50KG급, 60KG급 등이 있다.
- 송유관용 : 고장력 및 극저온인성, 용접성이 우수한 강재로 원유 및 천연가스의 대량수송을 위한 수송용 강관, 유정관, 해양구조물용 강관 등 송유관 제작에 사용되고 있다. 주요제품은 API-5L B-L1, API-X52M-L2, API-X60M-L2, API-X70M-L2 등이 있다.
강관
강관은 열연강판을 원형관의 형태로 성형 후 전기저항용접 방식과 아크용접방식을 통해 다양한 규격(외형, 두께, 재직)으로 생산된다. 일반적으로는 원형이지만, 주문에 따라 사각형 등 여러 모양의 각형강관도 생산이 가능하다. 축적된 기술력으로 만들어진 현대제철의 강관제품은 건축기초재에서부터 사회 간접자본 시설에까지 널리 사용되며 국가산업화를 이끌어 왔다. 특히, 수도용 배수관, 도시가스관, 건축현장, 토목기초자제, 자동차, 선박부품 등 다양한 산업 현장에서 광범위하게 사용된다. 주요 제품은 배관용강관, 송유관, 유정용강관, 전산관, 구조용강관, 강관말뚝, 스테인리스강관 등이 있다.[2]
자동차 경량화 부품
자동차 경량화 부품은 자동차의 연비를 개선하고 배기가스를 줄이면서 동시에 안전도 향상까지 가능한 첨단공법을 적용한 제품이다. 현대제철의 자동차 경량화 부품은 핫스템핑(Hot Stamping: 고온에서 가열 후, 금형 내에서 성형과 동시에 급냉각해 초고강도 자동차 부품으로 제조), TWB(Tailor Welded Blank: 서로 다른 재질 및 두께의 판재를 재단 한 후, 레이저 용접으로 하나의 블랭크로 제조), 하이드로포밍(Hydro-Forming: 복잡한 모양의 자동차 부품을 만들 때, 용접하지 않고 강판을 튜브형태로 만든 뒤 안으로 강한 수압을 가해 원하는 형상대로 최종 제품을 제조) 공법을 이용해 생산하고 있다.[2]
철근
철근은 표면에 축 방향의 돌기와 횡 방향으로 일정한 간격의 마디가 있어 콘크리트 부착력이 강하게 만들어진 제품이다. 주로 건축, 토목구조용으로 많이 쓰이며 현대제철 D10~57mm에 이르는 다양한 규격의 철근을 당진제철소, 인천공장, 포항공장에서 생산하고 있다. 현대제철은 구조물의 안전과 품질 향상을 위해 고성능, 고기능 친환경 철근제품을 개발·생산하고 있다. 특히 용접용 철근, 초고장력 철근(SD 500/600), 나사형 철근, 내진용 철근 등과 같은 고부가가치 제품의 판매를 확대하고 있다. 최근에는 저가수입산 제품이 국내 시장을 잠식하고 있음에도 불구하고 시장 점유율을 확대해 나가고 있다.[2]
- 초고강도철근 : 항복강도가 50kg/mm2 이상의 특성을 지닌 제품입니다. 초고층 건물 및 초장대 교량 등 특수구조물에 사용되며 최근 수요가 증가하고 있다. 주요제품은 SD500, SD600, SD700 등이 있다.
- 일반(이형)철근 : 단면이 원형이면서 길이가 긴 봉강형태의 제품으로 표면에 마디(리브)가 있어 건축 공사 시 콘크리트와 물리적으로 원활하게 결합해 철근 콘크리트 건축물의 강도를 높이는 역할을 한다. 주로 건축자재 및 토목 구조용으로 사용되며 우리가 일상생활에서 가장 쉽게 접할 수 있는 제품이다. 주요제품은 SD300, SD400 등이 있다.
- 나사형철근 : 일반철근과 달리 종방향 마디가 없고, 나사와 같이 나선방향으로 마디가 형성되어 있는 제품이다. 일반철근과 달리 조립시 커플러를 이용해 연결의 경제성과 안정성이 높아 ‘선 조립, 후 시공’을 많이 하는 초고층 건물 등에 많이 쓰이는 제품이다. 주요제품은 SD400, SD500, SD600 등이 있다.
- 내진용철근 : 일반철근과 달리 강도의 상한치가 제한되어 있는 제품이다. 지진발생 시, 설계자가 의도한대로 움직여 건축물의 내진성능을 확보하는 역할을 한다. 이 제품은 연신율이 우수해 내진설계 건축물 외에 다양한 구조물에 적용되고 있다. 주요제품은 SD400S, SD500S 등이 있다.
- 용접용철근 : 일반철근과 달리 탄소함량과 탄소당량(Ceq)을 최적화하여 설계한 제품이다. 용접이 필요한 구조물에 용접성능의 보증을 위해 철근이음용으로 사용되고 있다. 주요제품은 SD400W, SD500W 등이 있다.
형강
형강은 단면의 형태가 일정하도록 압연해 만든 철강제품을 총칭해 일컫는 말로 주로 사용된다. 형강은 철스크랩을 전기로에 녹여 만든 쇳물로 연주작업을 거쳐 제조된 반제품의 빔블랭크, 블룸, 빌릿을 각각 1,000˚C 이상으로 가열한 뒤 압연해 만들어 진다. 이 때 만들어진 형강은 단편의 형상에 따라 봉강, H형강, I형강, T형강, ㄱ형강, ㄷ형강 등으로 분류된다. 형강은 강도와 충격 흡수력이 뛰어나기 때문에 건축 구조물의 주요구조재료와 주택 건설과 지하철, 교량의 기초용 말뚝으로 주로 사용된다. 특히 현대제철의 H형강, 부등후 앵글, 강널말뚝 등은 지식경제부로부터 세계일류상품에 선정돼 우수한 품질을 대외적으로 인정받고있다.[2]
- H형강 : 단면의 형태가 H모양의 제품으로 대형 구조물의 골조나 토목공사에 널리 사용되는 대표적 형강제품이다. 열연·후판 등을 용접해 만드는 용접 H형강에 비해 내질이 균일해 강도가 우수한 특성을 지니고 있다. 주요제품은 KS D 3502, JIS G 3192, ASTM A6, DIN 1025, BS 4, AS/NZS 3679.1 KS F 4603 등이 있다.
- ㄱ형강 : 단면의 형태가 ㄱ모양의 제품으로 철탑 부재나 선각 보강재, 트러스 등 철강 구조물의 보강재로 널리 사용되는 형강제품이다. 주요제품 KS D 3502, JIS G 3192, EN 10056-1 등이 있다.
- ㄷ형강 : 단면의 형태가 ㄷ모양의 제품으로 산업기계 프레임, 철골조의 가새·트러스 등에 사용되는 형강제품이다. 일반적으로 H형강이나 I형강으로 구성되는 철골 구조물의 접합부에 다양하게 적용된다. 주요제품 KS D 3502, JIS G 3192, ASTM A6, DIN 1026-1 등이 있다.
- I형강 : 단면의 형태가 I모양의 제품으로 H형강과 형태가 유사하나 폭이 좁고 웹이 두꺼운 특성을 가지고 있다. 주로 화물이 이동하는 호이스트의 주행레일, 가이드레일 등에 사용된다. 주요제품은 KS D 3502, JIS G 3192, KS E 4002 등이 있다.
- 강널말뚝 : 단면의 형태가 U모양의 제품으로 토목·건축공사에서 물막이와 흙막이용 말뚝과 구조물의 기초공사 소재로 사용됩니다. 연결부위가 열쇠형, 직선형 등 여려가지 형태를 가지고 있다. 주요제품은 SY300, SY400 등이 있다.
- 철도레일 : 단면 형태가 I모양으로 아랫변의 폭이 윗변에 비해 넓은 형태의 제품이다. 철도차량이 이동하는 레일에 사용되고, 다른 형강에 비해 강도가 높으며 내마모성이 뛰어난 특성을 지니고 있다. 고속철도용 레일, 자기부상열차용 레일 등이 있다. 주요제품은 50KGN, UIC60, KR60, 50NHH340, 50NHH370, 0KRH340, 60KRH370 등이 있다.
특수강
특수강은 크랭크샤프트, 콘로드 및 각종 기어류 등 자동차 핵심 부품에 주로 사용되는 제품으로 고강도와 고내구성이 요구된다. 현대제철은 연산 150만톤의 특수강 생산능력을 보유하고 있다. 또한, 불순물 함유량이 적은 탄소강과 함금원소를 첨가해 특성을 개량한 합금강 등 고품질 특수강을 봉강, 선재, 각강의 형태로 생산한다. 특수강 제품은 자동차용, 산업기계 및 농기계용, 중장비용, 조선용 등 다양한 분야에 적용된다.[2]
- 자동차용 : 주로 엔진, 파워트레인 등 엔진의 힘을 구동축에 이어주는 부품에 사용되는 제품으로 고강도와 고내구성의 특성을 지니고 있다. 첨가하는 합금에 따라 그 종류가 다양하며 단조, 인발 등의 후가공 및 열처리를 통해 구조용 부품으로 사용된다.
- 산업기계 및 농기계용 : 공작기계 및 트랙터 부품 등에 적용되며 자동차용 특수강과 특성이 유사한 합금강부터 탄소강까지 다양한 소재가 사용된다.
- 중장비용 : 굴착기의 엔진, 선회파트 뿐만 아니라 궤도를 연결하는 조립 부품인 핀, 부시, 링크 등에 사용된다. 일반적으로 탄소함유량이 높은 고경도, 내마모성이 뛰어난 소재가 사용된다.
- 조선용 : 굴착기의 엔진, 선회파트 뿐만 아니라 궤도를 연결하는 조립 부품인 핀, 부시, 링크 등에 사용된다. 일반적으로 탄소함유량이 높은 고경도, 내마모성이 뛰어난 소재가 사용된다.
중기계
무한궤도는 1,800년대 중후반에 고안된 것으로 처음에는 증기 트랙터나 마차바퀴가 진흙타에 빠지는 것을 막기 위한 것이었다. 현대제철은 부품에서 완제품에 이르기까지 무한궤도를 일괄 생산하는 세계 유일의 철강사이다. 현대제철은 지난 1985년 일본 건설중장비업체인 '일본 고마쓰'와의 기술제휴를 통해 굴삭기용 무한궤도를 개발, 국내외 주요 건설기계 생산업체에 제품을 공급하고 있다. 현대제철 포항공장에서는 수요의 대다수를 차지하는 20~40톤 급은 물론 90톤 급까지 양산할 수 있는 능력을 갖추고 있으며 연간 30만 톤의 무한궤도 생산능력을 보유하고 있다.[2]
- 무한궤도 : 험로에서 사용되는 굴삭기의 바닥 접지력을 높여 경사면 또는 험로에서 사용 할 수 있도록 고안된 엔진과 더불어 굴삭기성능을 결정하는 중요 부품이다.
롤
롤을 슬래브, 빌릿, 빔블랭크 등의 철강 반제품을 압연할 때 사용되는 제품이다. 압연기에 롤을 장착해 고온의 반제품을 압연하는데 사용되기 때문에 내마모성, 내열성, 내구성이 필수적이다. 현대제철의 압연롤은 열연, 후판, 봉형강 설립에 사용되고 있으며 국내 뿐만 아니라 해외 철강사에서도 품질을 인정받고 있다. 특히 열간압연용 원심주조공구강롤(HSS Roll)은 세계일류상품으로 선정됐다.[2]
- 열연 롤 : 고온의 슬래브를 압연하는데 사용되는 제품으로 열연제품 생산에 필수적이다. 열연의 평탄도 유지와 표면품질 확보에 주요한 역할을 하고 있다. 주요제품은 ADM (High Carbon Steel, Static & D/P), ICDP & E-ICDP (Enhanced Indefinite Chilled Iron, D/P), HCS & HCI (High Chromium Steel & Iron, D/P), HSS (High Speed Steel, D/P) 등이 있다.
- 후판 롤 : 고온의 슬래브를 압연하는데 사용되는 제품으로 후판제품 생산에 필수적이다. 폭이 넓고 두꺼운 후판을 생산하기 위해 주로 대형 사이즈의 ROLL이 많다. 주요제품은 ICDP & E-ICDP (Enhanced Indefinite Chilled Iron, D/P), HCS & HCI (High Chromium Steel & Iron, D/P) 등이 있다.
- 봉형강 롤 : 고온의 빌릿과 불룸을 압연하는데 사용하며, 생산 제품의 형태에 따라 다양한 단면이 있다. 주로 건축용 H형강과 철근 생산에 사용됩니다. 주요제품은 LCS (Low Carbnon Steel, Static ), ADM (High Carbon Steel, Static & D/P), DCI (Ductile Cast Iron, Static), HSS (High Speed Steel, D/P) 등이 있다.
스테인리스강판
스테인리스강(Stainless Steel)의 Stainless는 '녹이 슬지 않는다', '녹이 없다'를 의미한다. 크롬과 니켈 함급원소를 첨가해 일반상에 비해 월등한 내식성, 내마모성을 가지고 있으며 표면이 미려해 건축 내외장재, 엘리베이터, 주방기기 및 자동차 부품 등 여러 산업분야에 사용되고 있다. 현대제철은 인천공장에서 스테인리스 냉연강판을 고객의 요구에 맞는 두께로 상온에서 압연해 공급하고 있다.[2]
- 건축용 : 건축물의 내외장재로 사용되는 제품으로 표면이 미려하고 내식성 및 내지문성이 뛰어난 특성을 지니고 있다. 스테인리스 강판 표면에 착색 등 표면가공을 통해 다양한 형상의 제품이 생산되고 있다. 주요제품은 304, 430 등이 있다.
- 가전 및 주방용 : 가전제품의 내외장 소재와 위생성이 요구되는 주방용품에 사용되는 제품으로 내식성과 내마모성이 뛰어난 특징을 지니고 있는 제품이다. 일반적으로 TV프레임, 세탁기 내부 패널, 식기 등에 사용됩니다. 주요제품은 304, 304L, 316, 316L, 430 등이 있다.
- 자동차 용 : 자동차의 머플러, 연료탱크 등에 사용되는 제품으로 배기가스와 연료에 포함되어 있는 황 성분에 견디는 내산화성이 뛰어난 제품이다. 또한 자동차용의 경우 심가공이 많아 성형성이 뛰어난 특성을 가지고 있다. 주요제품은 304, 430, 439, 439L 등이 있다.
전략제품
자동차용 강판
가볍고 안전한 차는 모든 자동차 메이커의 최우선 과제이다. 현대제철은 일반 강판보다 2배 이상 강도가 높아 10% 가량 중량 절감이 가능한 초고장력 강판을 개발, 가볍고 안전한 자동차를 만드는데 기여하고 있다. 또한 강도가 높아지는 만큼 단단해지는 철의 물성을 고려해 강도와 가공성을 동시에 확보하는 기술 개발에 주력하고 있다. 현대제철은 '철강의 꽃'이라 불리는 자동차용 강판을 통해 자동차의 진화에 기여하고 있다. 제품특성으로는 자동차용 외판재같은 경우 표면 품질 및 성형 수준이 높은 강판품질 요구, 철저한 공정 및 품질 관리로 고가공성, 극저탄소, 고청정도 확보가 있으며, 자동차용 초고장력강판의 경우 고강도·고성형의 기술 요구, 신강종(TWIP강) 개발을 통한 가공의 한계 극복, 신공법 핵심기술 개발을 통한 생산성 증대 및 신규 차종 적용 범위 확대 등이 있다.[2]
초고강도 철근
현재 철근 콘트리트 구조물은 고층화, 대형화되고 구조 재료의 고강도, 고품질, 고기능화가 요구되고 있다. 특히 철근 콘크레트 구조의 뼈대 역할을 하는 철근의 경우 초고강도 철근의 수요가 더욱 가파르게 증가하고 있다. 현대제철의 초고강도 철근은 일반 철근과 비교해 강도가 높으면서 가공성과 용접성이 뛰어난 고성능, 고기능 제품이다. 이 철근을 사용하면 면적에 투입되는 철근량이 감소돼 공기단축과 건축비를 줄이는 효과를 볼 수 있다. 제품특성으로는 고성능 탄소당량 관리를 통한 품질향상 및 용접성능 확보, 충격을 흡수하는 연신률을 높여 건출묵 안전성 개선, 강재 사용량 절감으로 경제성이 높으며 시공 효율 향상 및 CO2 저감 등이 있다.[2]
건축구조용 H형강
최근 대형 지진이 자주 발생하면서 지진에 따른 피해를 최소화하고 예방하기 위한 건축 소재 개발이 전 세계적인 화두로 부각되고 있다. 국내 최고 전기로 제강 기술력을 보유한 현대제철은 1982년 국내 최초로 H형강을 생산한 이래 그동한 쌓아온 제품 노하우를 바탕으로 내진 성능을 갖춘 건축구조용 H형강(SHN, Steel 'H-sction' New)을 개발했다. 현대제철은 남극 장보고 과학기지 건설을 비롯해 콜롬비아 보고타 석탄화력발전소 건설현장 등에 국내 최초로 건축구조용 H형강을 공급하는 등 고성능 건축구조용 강재 시장을 선도하고 있다. 제품 특성으로는 충격 흡수 능력이 좋아 지진발생시 건축물의 안정성 개선, 강도 상한치를 제한해 설계자가 의도한대로 건축물 내진설계 효과 극대화, 최적 합금비율 관리로 일반형강 대비 용접부 신뢰성 향상 등이 있다.[2]
연구·개발
기술연구소
현대제철 기술연구소는 Application Engineering Center 로서 고객의 가치 향상을 위한 기술개발을 진행하고 있다.[2]
- 고객의 제품가치 향상을 위하여 High Performance Product를 개발한다
- 자동차 경량화를 위한 고강도/고성형의 맞춤형 자동차강판, 안전한 건축물을 위한 고강도 내진 형강/철근, 극한지용 기능성 에너지강재 개발 - 고객의 여유로운 삶을 위하고 편의성 향상을 위해 고객 맞춤형(Engineering) 기술을 개발한다.
- 최고의 자동차 부품/차체 성능 구현을 위한 고강도 강판 접합, 성형, 장청 기술 개발, 최고 효율의 초고층 건축물 구현을 위한 최신 공법 개발, 고강도/대입열 용접 기술 개발. - 품질에 대한 신뢰를 바탕으로 고객과의 동행을 위해 공정 자동화 기술을 개발한다.
- 빅데이터 활용 품질 예측 기술개발, 통합 모델 자동 조업 기술 개발, 설비 자동화 기술 개발 등 고객 요구에 따른 유연 생산/품질 체계 확보 - 인류를 위한 기여 및 책임을 다하기 위해 친환경/미래형 에너지 기술을 개발한다.
- 열설비 고효율화 기술, 저NOx 연소 기술, 폐열 발전 기술, 탄소 자원화 기술, LCA 기술, SOx/NOx/먼지 저감 기술, 제철소 부산물 재활용 및 폐수 무방류 통한 신 부가가치 창출.
연구·개발 분야
기술연구 분야
공정 제품 지원 환경 응용 선행연구 제선기술 자동차강판개발 기술전략 친환경기술 AE 기술(Application Engineering) 머신러닝기반 강종개발 제강기술 박판개발 제품기획 에너지기술 부품개발 경량소재 개발 열연기술 후판개발 재료분석 솔루션마케팅 냉연기술 전기로제품개발 기술인프라지원 표면처리기술 특수강개발 제품설계 특수강기술 철분말개발 제어계측기술 친환경자동차부품개발
제품개발 분야
- 자동차용 강재 : 현대ㆍ기아자동차와의 공동 연구를 통해 자동차용 초고장력 강판, 자동차 경량화 부품용 특수강 등의 고부가가치 제품 개발
- 해양구조 및 선박용 강재 : 기본적인 해양구조 및 선박용 강재뿐 아니라 혹독한 환경과 구조적 특성에 적합하도록 강도, 저온충격인성, 용접성능 등을 향상시킨 강재 개발
- 에너지 강재 : 높은 기술력을 바탕으로 원유와 가스 등의 채굴, 이송 및 저장 시설에 쓰이는 고부가가치 에너지 강재 개발
- 건축, 건설용 강재 : 오랜 시간 축척한 기술과 노하우를 바탕으로 안전한 건축, 편리한 설계를 위해 내진기능을 향상시킨 철근과 H형강 등 고성능 제품 기술 개발[2]
기초연구 분야
현대제철은 650여종 이상의 첨단 분석장비를 통해 원료 품질 분석, 제품 물성평가, 신제품 개발에 힘쓰고 있다. 또한 현대자동차그룹 및 고객사를 대상으로 한 종합 소재 분석센터 역할을 하고 있다.[2]
선행기술 분야
현대제철은 상용 철강제품 뿐만 아니라, 미래 가치를 창조해 나가기 위해 머신러닝을 이용한 신강종 개발, 경량화 신소재 개발 등 첨단 선행연구에 매진하고 있다.
- CFRP : 차량 경량화를 위한 탄소섬유강화복합재료(CFRP) 부품 연구 대량 생산 공법 적용 CFRP 부품 성형 및 제품화 기술 개발
- 전산모사 : 전산모사 통합환경 및 Machining Learning 방법을 활용한 신강종 및 경량 신소재 개발 연구 수행[2]
응용기술 분야
쇳물과 자동차의 중간 매개체 역할을 하는 응용기술을 통해 글로벌 경쟁력 강화 및 고객 솔루션을 제공하고 있다.
- 주요 연구분야 : 경량화 기술, 요소 기술 (성형, 용접, 방청), 해석 기술, 차체/샤시 기술[2]
친환경 신기술 개발
페수 방류수 재이용 기술
인류 미래를 위해 친환경 제철소를 구현하고자 노력하는 현대제철은 건설 초기부터 비산먼지를 저감하는 밀폐형 원료저장 및 이송 시설, 배출가스 및 슬래그 재활용 설비 등 많은 투자와 노력을 기울여왔다. 특히, 기후 온난화와 더불어 지속적인 용수 사용량 증가에 따른 전세계적인 물 부족 문제 해결을 위 폐수를 재이용하는 대체수자원 확보를 위한 기술개발을 진행해왔다. 제철소의 고로 및 코크스 제조 공정에서 발생하는 폐수는 고농도의 난분해성 유기물질과 무기 이온물질을 다량 함유하고 있어 물리화학적 처리 및 생물학적 처리를 하더라도 공정수로 재이용하기 어렵다. 현대제철은 이러한 악성 폐수를 멤브레인 기술을 활용하여 50% 이상 재이용하는 폐수처리 신공정을 개발하였으며, 장기적으로 모든 폐수를 재이용 하는 세계 최초 무방류 제철소 건설을 위해 역삼투 농축폐수 처리기술에 대한 연구를 진행하고 있다.[2]
슬래그 골재르 활용한 고부가 건설재료 개발
현대제철은 제강 슬래그를 이용한 아스콘 제품인 '펠로팔트(FerroPhalt)'를 개발하여 제철소 내부도로에 사용하고 있다. 전로나 전기로의 정련과정에 사용하는 석회석의 부산물로 발생되는 제강 슬래그를 이용한 친환경 도로 포장재 '페로팔트'는 철을 뜻하는 접두사 '페로(Ferro)'와 아스팔트(Asphalt)'를 조합한 이름이다. 페로팔트는 기동안 부산물로만 여겨져 왔던 제강 슬래그로 천연골재를 대체해 슬래그의 재활용 범위를 넓혔다는 데 의의가 있다. 특히 일반도로에 페로팔트가 본격적으로 활용된다면 연간 100만톤 이상의 천연골재를 대체할 수 있어 석산 개발로 인한 환경훼손 및 자원고갈 저감에도 기여할 수 있다. 현대제철은 2012년 페로팔트 개발에 착수, 2013년 당진제철소 사내도로에 천연골재 아스콘과 페로팔트를 각각 시공하여 3년간 내구성 비교 평가를 통해 내구성이 우수함을 확인했으며, 현재까지 5만톤 이상의 페로팔트 시공 실적을 통해 안정적인 품질과 시공기술을 확보하고 있다. 현대제철은 페로팔트에 이은 페로콘(FerroCon) 개발에도 박차를 가하고 있다. 고로 슬래그를 이용한 콘크리트 제품인 페로콘은 '페로(Ferro)'와 콘트리트(concrete)'를 조합해 만든 이름이며 현재 수로관이나 맨홀과 같은 콘크리트 2차 제품에 사용되고 있다. 향후에는 레미콘이나 PHC 파일 제품까지 확대에 활용할 예정이다.[2]
생산공정
고로
- 제선공장
철광석, 석탄 및 부원료 등을 밀폐형 컨베이어 벨트를 이용해 친환경저장시설인 원형, 선형저장고에 저장한다.
- 원료저장시설 : 항만으로부터 하역된 원료(철광석,원료탄)를 저장하는 곳으로, 분진 비산 및 오탁수 발생을 최소화하기 위해 밀폐형으로 건설한 친환경 시설.
- 원형저장고 : 최대 지름 130m, 높이 65m에 이르는 초대형 돔으로 철광석 저장고 4개 및 배합 저장고 3개로 구성
선형저장고 : 7개의 저장 시설로 폭 96~98m, 길이 215~615m에 이르며 석탄, 철광석 및 부원료를 비축
- 원형저장고 : 최대 지름 130m, 높이 65m에 이르는 초대형 돔으로 철광석 저장고 4개 및 배합 저장고 3개로 구성
철광석과 석탄을 이용해 소결광 및 코크스를 생산 후, 고로에 장입해 용선(쇳물)을 생산한다.
- 소결공장과 코크스 공장
- 소결공정 : 분철광석에 석회석 등의 부원료를 혼합 후 고온으로 가열해 소결광을 생산하는 곳
코크스 공정 : 석탄을 고온 건류해 코크스를 생산하는 곳
- 소결공정 : 분철광석에 석회석 등의 부원료를 혼합 후 고온으로 가열해 소결광을 생산하는 곳
- 고로공정과 토페도카
- 고로 : 코크스와 열풍의 연소를 통해 소결광을 녹여 용선(쇳물)을 생산하는 시설
토페도카 : 고로에서 생산된 용선을 제강공장으로 이송하는 특수 내화처리 차량
- 고로 : 코크스와 열풍의 연소를 통해 소결광을 녹여 용선(쇳물)을 생산하는 시설
- 제강공장
용선(쇳물)의 불순물을 제거하고 성분 조정을 통해 강종에 적합한 용강을 만들어 슬래브(반제품)를 생산한다.
- 용선예비처리기 : 전로에 용선(쇳물)을 장입하기 전 불순물인 ‘규소(Si), 인(P), ,황(S)’을 제거하는 설비
- 전로 : 산소를 넣어 산화반응을 통해 용선 내의 탄소(C)를 제거하는 공정
- 정련기
- LF 정련 : 아크열(전기 방전 시 발행하는 열)로 전로에서 나온 쇳물의 온도 조절 및 성분 조정을 하는 공정
RH 정련 : 진공처리를 통해 용상의 가스(산소,수소) 제거 및 성분을 조정하는 설비
- LF 정련 : 아크열(전기 방전 시 발행하는 열)로 전로에서 나온 쇳물의 온도 조절 및 성분 조정을 하는 공정
- 연속주조기 : 쇳물을 연속적으로 주조해 슬래브(반제품)를 만드는 설비
- 슬래브(반제품) : 열연, 후판 등의 제품을 생산하기 위한 중간 단계의 제품 (두께 225~300mm, 폭 900~2200m)
- 후판공장
슬래브(반제품)를 압연해 다양한 규격(두께, 길이)의 후판을 생산한다.
- 가열로 : 슬래브(반제품)를 압연에 필요한 온도까지 가열하는 설비
- 디스케일러 : 재료 표면에 생기는 산화철을 고압의 물을 분사해 제거하는 설비
- 조압연기 : 최종압연을 위한 준비 압열 설비
- 사상압연기 : 조압연 된 판재를 최종 제품 구격에 맞는 두께, 폭, 모양으로 조정하는 설비
- 냉각기 : 압연이 완료된 제품의 품질 향상을 위해 냉각수를 분사해 냉각하는 설비
- 절단기 : 고객의 요구에 맞게 길이, 폭을 절단하는 설비
- 열처리기 : 압연이 완료된 후판의 강도 및 인성을 증가시켜 고급강종의 후판을 생산하는 설비
- 열연공장
슬래브(반제품)를 압연해 다양한 규격(두께, 길이)의 열연강판을 생산을 생산한다.
- 가열로 : 슬래브(반제품)를 압연에 적합한 온도로 가열하는 설비
- 조압연기 : 최종압연(사상압연)에서 작업이 가능하도록 슬래브 두께와 폭을 적합한 치수로 압연하는 설비
- 사상압연기 : 조압연된 바(Bar)를 최종 제품의 규격에 맞는 두께, 폭으로 압연하는 설비
- 냉각기 : 압연이 완료된 판재를 최적의 냉각속도로 냉각해 원하는 기계적 성질을 확보하는 설비
- 권취기 : 열연강판을 쉽게 보관하고 운반하기 위하여 코일 형태로 만드는 설비
- 냉연공장
표면이 미려하고 가공성이 우수한 고품질의 냉연강판을 생산한다
- 연속산세압연설비(PL/TCM) : 열연강판의 표면에 부착되어 있는 산화물 등을 산세처리(염산 또는 황산)로 깨끗이 제거 후, 상온에서 원하는 두께로 만드는 설비
- - 공정순서
- 두 개의 코일을 용접해 강판의 형상교정을 거친다.
- 소정의 농도로 가열된 염산을 분사해 강판 표면의 스케일을 제거한다.
- 연속적으로 통과하는 강판의 가장자리를 절단한다.
- 5개의 스탠드로 연속 냉간압연하여 요구하는 두께로 조절한다.
- 압연 후 강판을 코일 형태로 권취한다.
- 연속소둔설비(CAL) : 열처리를 하지 않은 열연강판을 가열·냉각작업을 반복해 강판의 가공성을 개선하는 설비
- - 공정순서
- 냉간압연된 강판을 전해탈지를 통해 표면에 붙어있는 이물질을 제거하고, 세척 후 건조시킨다.
- 압측저장설비에서 코일의 추가 장입을 위해 정지하는 동안, 소둔로에서 연속 운전을 하기 위해 저장되어 있는 강판을 공급한다.
- 소둔로에서 고온으로 열처리를 한다.[2]
전기로
- 제강공장
철스크랩을 원료로 전기로 제강 공정을 거쳐 빌릿, 블룸, 빔블랭크 등의 반제품을 생산한다.
- 철스크랩 : 철스크랩은 전기로 조업의 원료로 폐차, 폐건축물 등에서 나오는 고철을 비롯해 철강 가공과정에서 나오는 선철 등을 뜻하는 용어
- 전기로 : 전극에 전류를 흐르게 만들어 전극과 철스크랩 사이에 발생하는 고온의 아크열을 이용해 쇳물을 만드는 설비
- 아크열 : 전기 방전 시 발생하는 열
- LF 정련기 : 전기로에서 나온 쇳물을 아크열을 이용해 온도를 조절하고 성분을 조정하는 설비
- LF (Ladle Furnace) : 쇳물을 정련하는 설비로 온도조절, 성분 균일화, 염기성 슬래그 형성을 통한 환원정련의 역할 수행
- 연속주조기 : 쇳물을 연속적으로 주조해 반제품을 제조하는 설비
- 반제품 : 최종 철강제품을 생산하기 위한 중간단계의 제품
- 빌렛 : 소형 봉형강, 선재, 강대 등의 재료로 사용(절단면의 한 변이 60~160mm, 길이 1~9m)
- 블룸 : 중/대형 봉형강, 빌렛, 시트바, 스켈프 등 소형 반제품 제조(절단면의 한 변이 130~430mm, 길이 최소 1~6m)
- 빔블랑크 : H형강을 만들기 위한 반제품으로 대형 봉형강, 시트파일(강시판) 등의 재료로 사용
- 형강공장
반제품을 압연, 교정, 냉각해 다양한 규격(두께, 길이)의 H형강 등을 생산한다.
- 가열로 : 반제품을 압연하기 좋은 온도까지 가열하는 설비
- 디스케일러 : 재료 표면에 생기는 산화철을 물의 압력을 이용해 제거하는 설비
- 조압연기 : 최종 압연을 위한 준비 압연 설비
- 사상압연기 : 두개의 롤에 힘을 가해 원하는 모양의 형강을 생산하는 설비
- 형강공장 : 거치는 압연기의 종류, 용도에 따라 형태와 길이를 다양하게 생산하는 시설(H형강, 강널말뚝, 레일 등)
- H형강: 현대제철이 국내 최초 개발한 자사 대표제품으로 구조물의 기둥,보,기타구조물 및 토목용 가설구조물로 사용
- 일반형강 : 단면형상에 따라 구분된 ㄱ형강, ㄷ형강, I형강 등 다양한 종류와 규격으로 트러스재, 조선, 철골구조 등으로 사용
- 철근공장
반제품을 압연, 냉각해 다양한 규격(두께, 길이)의 철근을 생산한다.
- 가열로 : 반제품을 천연가스를 이용해 압연에 필요한 온도까지 가열하는 설비
- 조압연기 : 최종압연을 위한 준비 압연
- 사상압연기 : 두 개의 롤에 힘을 가해 원하는 모양의 완제품으로 생산하는 공정
- 철근: 콘크리트 보강재로 건축 및 토목용 자재로 사용되는 철강재[2]
ESG 경영
ESG가 전 세계 경영 트렌드로 주목받고 있다. ESG는 환경(Environment), 사회(Social), 지배 구조(Governance)의 약자인 ESG는 기업의 비재무적인 성과를 평가하는 기준으로 쓰이고 있다. 기업이 환경을 보호하고, 사회적 가치를 중요하게 여기며 투명하고 윤리적인 지배 구조를 갖출수록 지속해서 성장할 수 있다고 전망된다. 기업이 환경을 생각하고 사회적인 책임을 이행할수록 성과 지표에도 긍정적 영향을 준다는 점이 확인되면서 모든 산업군에서 ESG 경영을 실천하고 있다. 친환경 제철소의 모습도 점점 계속보이고 있다. 철광석은 지구 질량의 32%를 차지할 만큼 매장량이 풍부한 자원이다. 눈길을 우주로 돌려도 가장 쉽게 발견할 수 있는 금속이다. 구리나 알루미늄과 달리 톤당 함유량이 높아 많은 양을 채굴해도 자원 고갈의 우려가 적다. 특히 철 제품은 100년 이상의 수명을 가지고 있고 재활용이 용이하다는 특장점이 있다. 1톤 당 재생가능 횟수는 40번 이상이다. 인류가 철을 다룬 역사는 100년이 넘지만 '탄소 배출'과 '안전 문제'는 해결해야 할 숙제다. 철은 생산과정에서 필연적으로 탄소를 배출시킨다. 고윤에서 철을 용해하는 과정을 거쳐야 하기 때문에 화재 등 사고 발생 위험도 높다. 국내 최대이자 최초의 전기로 제강사인 현대제철은 안전을 지키면서 오염도는 낮추는 친환경 기술을 선보이고 있다. 탄소 기업이라는 부정적 꼬리표를 떼고 친환경 기업으로 전환한다는 최고 경영진의 의지가 반영된 결과이다. 현대제철은 제철소의 친환경화를 위해 2009년 세계 최초로 밀폐형 원료처리시설을 도입했다. 철광석과 석탄은 대부분 가루 상태로 되어 있는데, 바람이 불면 가루가 날려 지역 환경에 영향을 미치게 됩니다. 이를 방지하기 위해 현대제철은 밀폐형 원료 처리장 건설을 고안했습니다. 대형 선박을 통해 철광석과 유연탄 등의 원료가 운송되면 밀폐형 연속식 하역기와 벨트 컨베이어를 이용해 외부 노출 없이 철광석과 유연탄을 옮기는데, 이 시설은 바람이 심한 임해(臨海) 제철소의 비산먼지를 획기적으로 절감시켰으며, 기존 개방형 원료처리시설보다 기상 조건에 따른 제약이 없고, 다량의 원료를 보관할 수 있어 원료 관리 비용도 줄일 수 있게 되었다.[17] 또한, 현대제철은 당진제철소 안에 제선, 제강, 압연 공정을 모두 갖춘 일관제철소를 완공하고, 세계 최초로 자원순환형 철강 시스템을 구축했다. 고로에서 철광석을 녹여 만든 철은 자동차, 배, 각종 전기제품의 소재로 쓰인다. 철강 제품의 마지막 단계 산물인 철 스크랩(고철)도 쓰임새가 많다. 고철은 교량이나 건축용 철강의 원부자재로 재활용된다. 현대제철은 철 스크랩을 모아 연간 1000만톤 이상의 형강과 철근 제품을 생산하고 있다. 철 스크랩은 철광석, 석탄 등 다른 제강 원료와 비교해 이산화탄소를 비롯 오염원의 배출이 상대적으로 낮다. 현대제철은 2020년 산업통상자원부 산하 국가기술표준원으로부터 철 스크랩 재활용의 친환경성을 인정받아 GR(Good Recycled)인증을 획득했다. 2019년 이 회사의 형광·철근 제품은 한국 환경부, 미국UL 환경인증을 각각 획득했다. 국내 전기로 운영 제철기업 중 최초의 성과이다.[18]
2021년 3월, 이러한 노력과 비전을 알리는 영상을 공식 유튜브에 공개했다. 일러스트와 애니메이션 기술을 이용한 영상 제작 방식인 모션그래픽기법을 사용해 일반인들도 친근하게 친환경 제철 기술을 이해할 수 있도록 만들었다. 이번에 공개된 모션그래픽은 고로 브리더(breather) 편이다. 고로는 철광석에서 철을 만들 때 사용되는 탑 모양의 가열로를 말한다. 최대 2,300도의 고온고압으로 철광석을 녹여 청정 쇳물을 만들어내는 곳이다. 고로가 너무 뜨거워지면 폭발 위험이 있기 때문에 1년에 8번 고로의 최상단 안전밸브인 브리더를 열고 있다. 오염물질이 배출될 가능성은 있었지만, 안전을 위해서 해야 하는 일이었기 때문에 고민이 많았다. 고로 브리더 문제는 세계의 모든 제철 회사들이 가진 고민거리였다. 현대제철은 이 문제를 해결하는 데에 앞장섰다. 세계 유수의 엔지니어링 기술 회사인 네덜란드 기업 다니엘리 코러스와 협력해 고로의 오염물질 배출량을 줄일 수 있는 ‘가스 청정 밸브’를 개발했다. 안전을 지키면서도 깨끗한 철을 만들 방법을 생각해 낸 것이다. 가스 청정 밸브는 고로가 배출하는 유해가스를 줄일 수 있는 세계 최초의 설비이다. 고로가 작동하고 있을 때 외부 공기 유입을 방지하는 스팀 주입 시설을 활용했다. 원래 고로는 내부 압력을 조절하고 외부 공기 유입을 막기 위해 외부 저장소에 있던 가스를 가스의 수분을 줄이는 탈습설비와 가스의 불순물을 모으는 집진설비를 통해 증기 형태로 주입하도록 만들어져 있다. 가스 청정 밸브 시설은 해당 설비를 고로 오염 물질에 활용하는 방법으로 개발됐습니다. 고로의 오염 물질을 탈습설비와 집진설비를 거쳐 정화하고, 정화가 완료된 물질은 추가로 설치한 가스 청정 밸브를 통해 배출되는 원리이다. 가스 청정 밸브는 현재 당진제철소 1~3 고로에 설치되어 있는데, 고로의 환경 설비인 만큼 국내 및 해외 제철소가 설치를 원할 경우 적극적으로 기술을 지원할 계획이다. 환경을 생각하는 현대제철의 노력을 알리기 위한 모션그래픽은 현대제철이 그리는 수소사회, 철의 재활용 등을 주제로 추가 공개될 예정이다. 이외에도 현대제철 곳곳에는 환경을 생각하는 기술이 숨어있다. 고농도의 난분해성 유기물질과 무기 이온 물질을 다량 함유해 공정수로 재사용하기 어려웠던 악성 폐수를 50% 이상 재이용할 수 있는 기술을 개발해 활용하고 있다. 또, 현대제철의 내부 도로에는 페로팔트라는 소재가 적용되어 있는데, 페로팔트는 현대제철에서 제강 슬래그를 재활용해 만든 친환경 도로 포장재이다. 제강 슬래그는 고온의 전기로에서 철을 만들 때 생기는 비금속 물질과 금속 산화물을 말한다. 페로팔트의 개발로 과거 찌꺼기로만 여겨졌던 제강 슬래그의 재활용 범위가 넓어졌다. 일반도로에 페로팔트가 활용된다면 연간 100만 톤 이상의 천연골재를 대체할 수 있어 환경 보호에 도움이 될 것이다. 고로 슬래그를 이용한 콘크리트 제품인 페로콘도 개발해 수로관이나 맨홀에 사용 중인데, 지속적인 연구와 개발을 통해 적용 제품군을 더 확대할 예정이다.[17]
수소는 현대제철의 또 다른 미래산업이다. 현대제철은 당진제철소 코크스 제조공정과 전로공정에서 발생하는 부생가스 속 타르, 황, 벤젠 등 유해물질을 걸러 수소를 추출한다. 이 때 추출된 수소의 순도는 99.999%다. 부생수소의 절반은 자동차 충전과 반도체 정밀 클리닝 공정에 각각 쓰인다. 나머지 절반은 제철소에서 제품의 산화 방지 용도로 사용한다. 현대제철은 2025년까지 수소생산량을 10배 이상 늘릴 계획이다. 현재 연간 3500톤의 부생수소를 생산하고 있는데, 연간 4만톤 규모까지 수소생산을 확대하는 것이 목표다. 이는 수소전기차 약 20만대가 1년 동안 달릴 수 있는 양이다. 한편 현대제철은 수소시대에 맞춰 친환경차용 강종부터 특수부품 개발에 나서고 있다. 기존 내연기관의 엔진과 변속기에 쓰이던 특수강을 대체해 구동모터와 감속기용 제품을 새롭게 내놓았다. 이를 위해 연구개발비를 매년 1100~1400억원으로 늘리는 등 투자를 확대할 계획이다. 회사는 지난해 자동차용 신제품 6건을 출시했으며 총 266종의 자동차 강종을 개발했다. 연간 1만6000대 규모의 수소전기차용 금속분리판도 생산한다. 금속분리판은 외부에서 공급된 수소와 산소의 화학반응 발생을 차단한 뒤, 각 전극 내부로 공급하는 부품이다. 전극막 접합체(MEA)와 함께 수소전기차용 연료전지의 핵심 기술로 꼽힌다. 현대제철은 2013년부터 금속분리판 양산기술 개발을 시작해 18년 대량생산에 성공했다. 회사의 공장 설비는 설계부터 생산까지 전 과정이 국내 기술로 이뤄져 있다.[18] 현대제철은 친환경 모빌리티에 적용할 수 있는 신기술도 적극적으로 개발 중이다. 친환경 자동차를 위한 자체 브랜드 H-솔루션(H-SOLUTION)을 선보였다. 초고강도 경량 차체를 실현하겠다는 의지가 담긴 H-솔루션은 고장력강과 핫스탬핑 등의 자동차 소재와 품질을 높일 수 있는 물성/성형/용접/도장/부품화 등을 아우르는 서비스를 제공하고 있다. 친환경차는 내연기관차와 구동 시스템이 다르기 때문에 차체 구조에도 많은 차이가 있는데, 현대제철은 H-솔루션을 활용해 전기차 전용 플랫폼에 맞는 소재 발굴과 부품화 기술 확보로 고객에게 최적화된 자동차 소재를 빠르게 제공할 수 있도록 노력하고 있다. 예를 들어 자율주행차의 상용화가 이뤄져 핸들이 필요 없어지면 차량 공간의 개념이 바뀌어 시트나 센터 필러 구조가 변화할 텐데, 바뀐 차량 구조의 충돌 안전 성능을 확보하려면 기존과는 다른 개념의 보강 설계가 필요할 것이다. H-솔루션은 이러한 미래 모빌리티에 대비해 차체, 도어 등의 초고강도 소재를 적용한 기술을 특화하고 있다. 친환경을 위해 현대제철은 다양한 노력을 기울이고 있다. 전 세계적으로 철강 산업의 친환경화가 급속도로 진행되고 있는 만큼 현대제철도 비산 먼지 절감 기술부터 고로 오염물질 정화 기술, 미래 모빌리티 플랫폼에 적용되는 소재 등을 개발하며 꾸준히 지구를 살리는 일에 동참하고 있다. 앞으로도 현대제철은 건강한 지구를 만들기 위해 다양한 친환경 캠페인을 진행할 계획이다.[17]
현대제철이 현대차그룹의 ESG(환경·사회책임·지배구조) 경영에 발 맞춰 자정적 역할을 강조하고 있다. 무엇보다 외형적 성장에 집중했던 과거와 달리 스스로 변화를 모색하고 있다는 평가다. 2021년 2월 24일 업계에 따르면 현대제철은 2021년 3월 23일 열리는 주주총회에서 장금주 서울시립대 경영학 교수를 사외이사로 선임하는 안건을 상정했다. 장 교수는 세금 관련 논문을 집필하는 등 회계·세무 분야 전문가로 알려져 있으며 한국윤리경영학회 수석부회장을 겸임하고 있다. 이번 결정은 사외이사를 통해 윤리경영을 강화하겠다는 현대제철의 의지로 풀이된다. 현대제철이 여성 사외이사를 선임하는 것은 창립 이후 처음이다.현대제철은 ESG 경영 실천을 위해 사내에 투명경영위원회와 안전·환경 자문위원회, ESG 거버넌스, ESG 실장협의체, ESG 실무협의체 등을 설치·운영 중이다. 현대제철 21개 부서가 참여한 ESG 거버넌스는 의사결정부터 실행, 점검을 총괄하는 체계를 구축하고 있다. 투명경영위원회는 사회공헌과 준법 활동 등을 심의하고, ESG 관련 주요 정책을 결정한다. 2019년 안전사고 재발을 막기 위해 출범한 안전·환경 자문위원회는 사회적 갈등 사안과 산업안전 분야 현안을 다루고 있다. 위원회는 학계와 법조계, 안전·환경 및 보건 분야 전문가로 구성됐으며 초대 자문위원장은 김지형 전 대법관이 맡았다. 현대제철은 지난해 위원회 인원을 19명으로 늘리고 10차에 걸쳐 자문위원회를 개최했다. ESG 실장협의체는 반기에 한 차례씩 전체회의를 열어 환경, 사회, 경제분과 별 실적을 점검한다. 실무협의체는 연간 3회에 걸쳐 환경정책, 온실가스 대응, 지속가능경영 관련 과제를 실행한다. 이들 조직은 ESG 경영의 이념과 기준, 가치 등이 현장에 착근하는데 상당한 성과를 내고 있다. 회사는 이들 시스템을 통해 ESG 관련 이슈에 적극 대응하고 있다. 2020년에는 코크스를 냉각할 때 발생하는 폐열을 모아 전력을 생산하는 코크스 건식소화설비(CDQ)를 도입했다. 회사는 2024년까지 총 3400억원을 투자해 탄소배출을 연간 50만톤 감축한다는 로드맵을 수립했다. 폐열을 이용한 자체 전력 생산도 계획 중이다. ESG 경영을 위한 투자도 성공적으로 유치했다. 회사는 지난달 사회적 책임투자를 목적으로 발행한 '녹색 채권'을 통해 5000억원을 모았다. 8200억원 상당의 ESG채권 발행에 성공한 LG화학에 이어 두 번째로 큰 액수다. 회사는 준법경영 풍토 확산을 위한 프로그램도 적극 시행하고 있다. 현대제철의 공정거래 자율준수 프로그램(CP) 현황에 따르면 내부거래, 하도급법 등을 주제로 한 사내교육은 모두 5차례 열렸다. 컴플라이언스 간행물도 월 2회 배포하는 등 전 직원이 준법경영의 가치와 필요성을 체감할 수 있도록 입체적인 프로그램을 운영하고 있다. 이밖에 현대글로비스, 현대오토에버, 이노션 현대차그룹 계열사와의 수의계약 내용이 공정거래법에 위반되는지 여부도 자체 점검하고 있다.앞서 2002년 현대제철은 '공정거래 자율준수 프로그램'을 도입했다. 법 위반을 사전에 예방하고 현대차그룹의 투명경영 이미지 제고하겠다는 취지다. CP는 기업들이 스스로 시장질서를 지키기 위해 도입한 지침이다. 공정위는 CP 등급결과에 따라 직권조사 면제, 제재처분 수위 감경 등의 인센티브를 제공하고 있다. 안동일 현대제철 사장은 CP 선포문에서 “지금까지 최대 생산, 최대 매출 등 외형적 규모와 양적 성장에 집중한 환경 속에서 공정거래는 최우선 선택지가 되기 어려운 측면이 없지 않았다”고 했다. 그러면서 “공정거래 준수를 포함한 준법의식은 현대제철이 선택해야 할 최우선 척도이며 우리가 나아가야 할 올바른 길을 알려주는 이정표”라고 강조했다.[19]
현대제철 2020년 통합보고서가 국제무대에서 수상하며 회사 비전과 미래 방향성을 인정받았다. 현대제철은 2021년 2월 22일 미국 커뮤니케이션 연맹(League of American Communications Professionals,LACP)이 주관하는 LACP 비전 어워즈에서 통합보고서 2020 Beyond Steel이 금상을 수상했다. LACP는 미국의 커뮤니케이션 분야의 전문가들이 설립한 글로벌 홍보·마케팅 전문기관이다. 2001년부터 매년 전 세계 기업, 정부기관, 단체 등을 대상으로 연차보고서, 지속가능경영보고서 등 커뮤니케이션 분야 자료를 심사해 시상하고 있다. 이번 대회에는 20개국 1000여개의 기업, 정부기관, 비영리단체 등이 참가했다. 이 가운데 우수 보고서를 뽑아 대상(Platinum), 금상(Gold), 은상(Silver), 동상(Bronze)으로 나눠 시상했다. 2020 Beyond Steel은 통합보고서 부문 첫인상, 표지 디자인, 최고 경영자 메시지, 내용 구성, 재무 보고, 창의성, 내용의 명확성, 정보 전달력 등 총 8개 평가항목 중 6개 항목에서 만점을 받아 총점 100점 만점에 98점을 획득했다. 현대제철은 지난 2016년부터 각각 발간됐던 지속가능경영보고서와 연차보고서를 결합해 ESG 정보공개 대응을 위한 통합보고서 형태로 발간하고 있다.이번에 수상한 통합보고서는 ESG 주요 성과를 이해관계자 요청에 맞춰 최적화했다. 사회적 가치를 정량 데이터로 공개하는 등 현대제철의 지속가능경영 중장기 전략을 체계적으로 담았다. 회사 관계자는 "지속가능경영 메시지를 담은 통합보고서가 좋은 성과를 거둬 기쁘다”며 “이번 수상을 통해 현대제철과 이해관계자의 소통이 더욱 활발해질 것으로 기대한다”고 말했다.[20]
현대제철이 극저온에도 견딜 수 있는 강종을 신규 개발해 이를 LNG(액화천연가스) 추진선에 공급한다.현대제철은 지난 5일 현대중공업이 건조 중인 LNG추진 컨테이너선 연료탱크용 소재에 대한 수주계약을 체결했다고 9일 밝혔다. 이번에 계약한 연료탱크용 소재는 지난해 12월 개발을 완료한 9% Ni(니켈) 후판이다.현대제철이 개발한 9% Ni 후판은 영하 196도의 극저온 환경에서도 충격에 대한 내성이 뛰어나고 용접성능이 우수해 LNG 연료탱크 등에 사용되는 초고성능 강재다.LNG는 기존 선박용 디젤에 비해 오염물질 배출이 현저히 적다는 장점이 있지만, 저장시설 내부를 영하 165℃ 아래로 유지해야 하는 등의 기술적 제한이 따른다.현대제철은 2018년 9월부터 9% Ni 후판 신강종에 대한 개발에 착수해 R&D 역량을 집중한 결과 지난해 3월 안정적인 품질 수준을 확보했다. 이어 12월에는 KR(한국), ABS(미국), DNVGL(노르웨이/독일) 등 국내외 주요 9대 선급인증을 모두 획득하는 한편, 같은 시기에 현대중공업의 고객사 평가까지 모두 완료하며 수주를 위한 준비를 마쳤다.이번에 계약된 수주 물량은 LNG추진 초대형 컨테이너선 2척분이다. 현대제철은 이번 수주를 시작으로 LNG추진선 연료탱크에 대한 추가 수주는 물론, LNG 플랜트와 LNG 터미널에 쓰이는 육상용 저장탱크 수주에도 적극 나선다는 계획이다.현대제철 관계자는 “세계적으로 환경규제 수준이 점차 강화됨에 따라 오염물질 배출이 적은 LNG에너지의 수요가 점차 증가하는 추세”라며 “이번에 납품하는 9% Ni 후판뿐 아니라 극저온 철근 등 초고성능 강재들을 앞세워 LNG 관련 시장을 계속 공략해 나가겠다”고 말했다.주요 증권사 리포트에 따르면 2020년 국내 조선사의 LNG추진선 수주는 129척이었으며, 2023년엔 1500척에 이를 것으로 내다보고 있다. 이는 전 세계 선박 예상 발주량의 약 67%에 이르는 수치다.또 우리나라 제9차 전력수급기본계획에서 2034년 LNG 설비용량 비중은 30.6%로, 석탄 비중이 축소되고 신재생에너지 비중이 확대되는 에너지 전환 시기에 있어 LNG가 가교 역할을 할 것으로 전망하고 있다.한편 현대제철은 지난해 12월 한국가스기술공사와 국내외 플랜트 사업 수주 경쟁력 강화를 위한 전략적 업무협약(MOU)을 체결한 바 있다. 이 협약을 통해 현대제철은 LNG플랜트 분야의 기술협업은 물론, 관련 강재 판매확대 효과도 기대하고 있다.[21]
2021년 2월 1일 현대제철은 기존 지표 중심의 생산·품질 관리에서 소비자 중심의 품질 관리로 전환하기 위해 전사적 혁신 활동인 전사 클레임 캠페인을 추진한다고 밝혔다. 현대제철은 세계 각국의 보호무역주의 확산에 따른 수출 시장 악화로 경쟁이 심화하고 코로나19로 주요 수요산업 침체가 장기화하며 경쟁력 제고를 위한 전사적인 혁신 필요성이 대두됐다며 캠페인 추진 배경을 설명했다. 전사 클레임 캠페인은 성과관리의 척도로 쓰이는 핵심 성과지표인 KPI(Key Performance Indicator) 중심의 품질 관리와 사후 조치 위주의 업무에서 벗어나 사전에 소비자와 시장의 요구를 분석해 품질 관리 체계를 재점검하고 개선하는 데 전사 역량을 집중하는 것이 핵심이다. 우선 현대제철은 소비자 중심 생산 및 품질 관리로 변화, 전 부문 품질 마인드 고취, 소비자 중심 선제적 업무 프로세스의 3대 추진 전략을 세웠다. 이를 통해 현대제철은 전사 품질 마인드 고취, 소비자 활동 강화, 클레임 관리 정책 변화, 관리 프로세스 고도화 등 구체적 방안을 추진할 예정이다. 전사 품질 마인드 고취를 위해선 소비자 만족의 첫걸음, 품질에서 시작한다는 슬로건을 제정하고 품질 회의 진행시 품질 관련 사례의 발표·공유를 확대해 임직원의 의식 향상을 꾀하는 동시에 포상제도도 운영해 품질 의식을 한층 강화할 계획이다. 소비자 활동 강화를 위해선 정기 임원 방문 소비자의 목소리(VOC; Voice of Customer) 청취 프로그램을 운영해 핵심 소비자의 의견을 청취한다. 불만이 많은 파트너사에 대해선 엔지니어를 동반해 방문하는 등 소비자 요구 대응을 강화하기로 했다. 또 현대제철은 비대면 화상 프로그램을 통해 실시간 소비자 불만을 확인하는 웹 세미나를 개최하는 등 소통도 확대할 방침이다. 클레임 관리 정책 변화로는 성과관리 지표 중 소비자 품질 만족도 관리 지표를 신설해 소비자의 불만을 최소화할 계획이다. 또 소비자 만족도 조사 항목을 세분화해 부문별로 미흡한 사항을 개선할 수 있도록 했다. 관리 프로세스 고도화로는 수주에서 출하에 이르기까지 사내 프로세스를 개선해 각 부문별로 소비자 요구를 반영하도록 했다. 더불어 품질 개선 협의체를 운영해 전 부문 협업을 통한 소비자 대응 프로세스를 일원화하기로 했다. 현대제철은 전사 클레임 캠페인을 연중 운영해 2021년 12월 성과를 전사에 공유할 예정이다. 현대제철 관계자는 “전사 클레임 캠페인의 성공적인 정착을 통해 경영위기를 극복하고 글로벌 철강 시장을 선도할 것”이라고 밝혔다.[22]
2021년 현대제철은 MRO 전문 기업인 엔투비와 구매대행 협약을 체결했다고 18일 밝혔다.MRO는 유지(Maintenance), 보수(Repair), 운영(Operation)의 약자로, 기업과 산업시설에서 필요한 소모성 자재를 뜻한다. MRO 업무는 금액과 건수에 비해 업무효과가 낮고 번거로워 대기업들은 구매대행을 검토하는 추세다. 현대제철은 이번 협약을 통해 전기자재, 공기구, 철강설비 부품 등을 최적의 조건으로 조달할 계획이다. 철강업 특화 품목에 대해 구매대행을 추진해 조업 효율성을 높이고, 장기적으로는 회사 전체의 업무 효율성 향상도 기대하고 있다. 현대제철은 또 엔투비와 구매대행 사업을 통해 발생하는 수익금 일부를 출연해 사회공헌을 위한 기금으로 조성할 계획이다. 조성된 기금은 현대제철이 추진하는 제철소 인근 바다 환경개선·나무심기 행사 등 탄소중립 및 환경개선 활동을 비롯해 중소기업 작업 환경개선·제조설비개선 컨설팅 지원 등 동반성장 활동, 보육종료아동 기능인력 양성·기술, 학업 멘토링 등 사회취약계층 성장, 자립지원 등에 쓰일 예정이다. 현대제철 관계자는 “구매업무 효율화를 위한 중장기적인 개선전략으로 구매대행을 도입했다”며 “향후 구매 경쟁력 강화는 물론 회사의 ESG(환경·사회·지배구조) 활동 강화에도 보탬이 될 것”이라고 말했다.[23]
적절한 처리방법이 없어 환경 문제로까지 부각된 굴·조개 등의 껍데기인 패각을 제철소에서 재활용할 길이 열렸다. 현대제철은 패각을 가공해 만든 석회 분말을 제철소 '소결(燒結)' 공정에 활용할 방침이라고 2021년 7월 28일 밝혔다. 소결은 가루 상태의 철광석을 고로 투입에 적합한 형태로 만드는 공정이다. 철광석 소결 과정에서 석회석을 첨가하면 고로 공정에서의 생산성 향상, 연료비 절감 등의 효과가 있기 때문에 쇳물을 만드는 과정에서의 석회석 사용은 필수적이다. 현대제철은 지난 2014년부터 소결 공정에서 패각을 활용하는 기술 개발에 나섰으며 이후 조업 테스트를 거쳐 대체 가능성을 확인했다. 지난 2019년에는 여수 지역 패각 가공사인 여수바이오와 석회석 대체용 패각 생산 및 재활용환경성평가를 위한 협업을 진행하고 지난해 9월 모사실험을 통해 품질 및 환경에 대한 영향 평가를 마쳤다.현재 폐기물관리법에 따라 석회석 대체 활용에 대한 재활용환경성평가가 진행 중이다. 최종 승인기관인 국립환경과학원의 승인을 받으면 국내 최초로 제철소 패각 재활용이 가능해지는 것은 물론 기업·지자체·정부기관 협업을 통한 광역적 자원재활용의 모범사례가 될 것으로 기대된다. 현대제철은 석회석을 패각으로 대체함으로써 재활용 되지 않아 방치된 패각으로 인해 발생하는 환경문제 해결과 함께 석회석 사용량을 줄여 온실가스를 감축하는 효과도 예상하고 있다. 그동안 패각은 폐기물관리법에 따라 사업장 폐기물로 분류돼 활용이 제한되면서 방치로 인한 환경 문제를 야기했다.해양수산부에 따르면 매년 30만톤이 발생되는 굴 패각 중 일부만 사료나 비료로 활용되고, 나머지 약 23만톤은 그대로 버려지면서 현재 약 100만톤 이상이 방치돼 있는 것으로 추정된다.현대제철 관계자는 "패각 재활용은 환경 문제 해결 및 사회적 책임을 이행하는 현대제철의 ESG 경영 사례다"라며 "패각 재활용을 통해 기업이미지를 제고하고 경남·전남 지역의 패각 문제 개선에도 기여할 방침이다"라고 말했다.[24]
사고 및 논란
사고
현대제철 당진공장에서 50대 외주 노동자가 컨베이어벨트에 끼여 숨지는 사고가 발생했다. 앞서 당진공장은 지난 2007년부터 약 10년간 작업 중 사고로 노동자 33명이 숨진 바 있는 만성 산업재해 사업장으로 악명이 높았다. 여기에다 2017년 12월에는 고용노동부의 근로감독도 받아 340건의 위반사항이 적발되기도 했지만 사고가 또다시 일어난 것이다. 현대제철은 2019년 2월 21일, "원료 이송시설에서 컨베이어벨트를 정비하던 직원이 20일 사망하는 안타까운 사고가 발생했다"며 "고인과 유가족께 깊은 애도를 표한다"고 밝혔다. 이어 "무엇보다 소중한 인명이 희생된 점에 저희 모든 임직원은 말할 수 없는 슬픔에 고개 숙여 고인의 명복을 빈다"며 "현대제철은 관계기관의 조사에 적극 협조하고 다시는 이러한 사고가 발생하지 않도록 대책 마련, 안전점검을 최우선으로 하겠다"고 밝혔다. 우선 경찰과 소방, 정부 당국에 따르면 2019년 2월 20일 오후 5시 29분쯤, 당진제철소에서 A(51)씨가 철광석을 이송하는 컨베이어벨트 뒷면 고무를 교체하는 작업 중 인근 컨베이어벨트에 끼여 숨졌다.'4인 1조 근무'로 A씨와 함께 작업하던 동료는 "A씨가 고무 교체작업을 하다가 공구를 가지러 간다고 했지만 이후 보이지 않아서 찾아보니 숨져 있었다"고 진술한 것으로 알려졌다. 당국은 "A씨가 작업용 자재를 가져오는 과정에서 컨베이어를 밟고 내려오던 중 옆에 있는 컨베이어벨트와 풀리 사이에 협착한 것으로 추정한다"고 설명했다.이번 현대제철 사고는 앞서 지난해 충남 태안 화력발전소에서 컨베이어벨트를 점검하다 숨진 故 김용균 씨의 사고와 유사하다는 점도 있지만 '산업재해가 현대제철에서 만성적으로 일어나고 있다'는 점에서 비판의 강도가 높아지고 있다.현대제철 당진공장은 지난 2007부터 2017년 말까지 작업 중 사고로 노동자 33명이 숨졌다. 이번 사고까지 합쳐 34명의 노동자가 사망했다. 지난 2013년 5월에는 전로 제강공장에서 보수작업을 하던 하청업체 직원 5명이 아르곤 가스에 질식해 숨졌고 같은 해 11월에도 가스 누출로 1명이 사망했다. 이어 2014년에도 추락 사고가 잇따랐고 2016년 11월에는 하청업체 소속 30대 노동자가 컨베이어벨트에 끼여 숨졌다. 2017년 12월에도 20대 노동자가 정기보수 작업 중 기계가 갑자기 작동해 사망했다. 결국 고용노동부 산하 대전지방노동청 천안지청은 지난 2017년 12월, 대대적인 근로감독에 나섰다. 당국은 근로감독을 통해 총 340건의 산업안전보건법 위반 사항을 적발했고 이 가운데 75%인 253건을 검찰에 송치했다. 이어 사용중지 명령 사안 3건과 과태료 부과 사항 28건을 적발해 총 2,270만 원의 과태료를 부과했지만 1년여 만인 2019년 2월 또다시 사고가 난 것이다. 노동청의 근로감독은 당시에도 무용지물이라는 비판이 이어졌다. 금속노조는 현대제철의 2018년 시설물 개선 공사 계획에 포함한 내용을 지적했을 뿐 근로자가 사망하는 중대 재해의 원인이나 구조적인 규명은 없었다며 면죄부를 주는 근로감독이라고 지적했다. 이어 "현대제철 근로자의 건강을 위협하는 쇳가루 등 먼지에 대한 노출, 롤 가공 과정에서 오일 미스트 노출에 따른 호흡기 질병 유발 가능성 등의 문제는 노동 당국이 외면했다"며 "특히 지난 2017년 12월 13일 사망사고가 발생한 곳에서 작업표준조차 존재하지 않았던 근본적인 문제 등을 눈감아 줬다"고 규탄했다.[25]
논란
현대제철 사내하청업체 14곳이 2021년 7월 31일 원청과 도급계약 종료를 이유로 폐업한다고 예고했다. 원청의 직접고용을 요구하며 현대제철 자회사 현대ITC에 지원하지 않은 사내하청 노동자는 일터를 잃을 위기에 처했다. 현대제철이 양자택일 상황을 만들어 자회사안을 관철하려는 것이라는 해석이 나온다. 2021년 8월 2일 금속 노사에 따르면 지난달 현대제철은 자회사 현대ITC를 올해 9월 중 설립해 사내하청 노동자 7천여명을 고용하겠다 밝혔다. 금속노조 현대제철비정규직지회(지회장 이강근)는 불법파견 논란을 피하기 위한 꼼수라고 보고 자회사 채용공고에 지원하지 않기로 결정했다. 인성검사·영상면접·건강검진 등 채용절차는 4일 종료될 예정이다. 현대제철 사내하청업체 14곳은 2021년 7월 30일 지회에 공문을 보내 “2021년 8월31일부로 현대제철㈜와의 도급계약이 종료됨으로 인해 사업을 종료하게 됐다”며 “당사 전 직원들과 고용관계 또한 2021년 8월31일부로 부득이하게 종료된다”고 밝혔다. 지회에 따르면 미주테크㈜를 제외한 13곳의 도급계약 종료 예정일은 2022년 2월이었지만 계약 종료시점이 앞당겨졌다. 지회는 “이들 업체 상당수가 현대제철 혹은 현대자동차그룹 전 임원이 운영하는 업체로 알고 있다”며 “현대제철은 남은 사내하청업체 18곳과도 계약종료 시기를 협의하고 있는 상태”라고 전했다. 이 과정에서 사내하청업체 노사가 맺은 단체협약 내용은 종잇조각이 됐다. 40개(이 중 8곳은 환경·시설·운송업무 수행으로 자회사 전환 대상에 미포함) 사내하청업체 노동자가 가입해 있는 지회는 매년 집단교섭을 진행해 왔다. 2021년 3월 노사 대표가 체결한 특별합의서에는 회사는 기업 합병·양도·이전·분할매각·사업 종료·도급계약 종료의 경우 조합에 사전 2개월 전 통보한다고 명시돼 있다. 이강근 지회장은 “노사 특별합의 사항을 포함해 단체협약을 전체적으로 위반하면서 자회사를 추진하는 상황을 보면 (현대제철의) 다급함이 느껴진다”며 “현대제철은 당사자인 비정규직지회와 직접 논의해야 한다”고 주장했다. 현대제철 사내하청업체 14곳 폐쇄로 일자리를 잃게 될 노동자 규모는 명확하지 않다. 해당 업체 노동자 중 누가 자회사에 지원했는지 여부가 확인되지 않기 때문이다. 다만 현대제철이 9월 현대ITC 출범 이후 순차적으로 남은 사내하청업체 18곳까지 폐쇄할 경우 자회사에 지원하지 않은 최소 2천여명이 갈 곳을 잃을 수 있다. 노조와 사측의 설명을 종합하면 지난달 현대ITC 채용공고에 전체 대상자 7천여명 중 최소 4천500명(인천·포항공장 각 1천명 포함)이 지원한 것으로 예상되는 상황이다. 이강근 지회장은 “자회사로 가기 전 조건이 근로자지위확인 소송 취하와 부제소합의”라며 “불법을 저지르더라도 고소고발을 진행하지 않겠다는 약속을 하라는 것으로, 불법이 없어지거나 해소되지 않는 것”이라고 비판했다. 현대제철쪽은 18개 사내하청업체의 계약종료 시점을 묻는 질문에 “업체마다 계약기간이 달라 확인하기 어렵다”고 밝혔다. 한편 대전지방고용노동청 천안지청은 최근 불법파견 혐의가 없다고 판단했던 현대제철 사내하청업체 10곳과 2개 공정(컨베이어벨트 수리·슬래브 야드 출하) 재조사를 시작했다. 이번 감독 대상에는 이달 말 폐업하겠다고 예고한 업체 네 곳이 포함돼 있는 것으로 알려졌다. 2020년 12월과 2021년 2월 고용노동부가 직접고용을 명령한 현대제철 사내하청 노동자는 모두 1천265명이다. 당진공장 노동자 3천228명은 근로자지위확인 소송을 진행 중이다. 2심에서 승소한 순천공장 노동자 157명은 대법원 판결을 기다리고 있다.[26]
현황 및 전망
현황
현대제철이 지난해 코로나19(COVID)로 인한 실적 부진을 떨치고 2021년엔 고부가가치제품 위주로 수익성을 높일 계획이다. 2021년에도 사업구조를 효율화하고 자동차강판 시장에서의 경쟁력 강화를 위해 신규강종 개발에 집중 투자한다. 현대제철은 2021년 1월 28일 실적발표 콘퍼런스콜을 통해 2020년 연결 기준 매출액은 전년인 2019년 대비 12.1% 감소한 18조234억원, 영업이익은 78% 감소한 730억원을 기록했다고 밝혔다. 현대제철은 실적에 대해 "코로나19의 영향으로 글로벌 경기는 물론 국내 수요산업이 전반적으로 위축됐으며 사업구조 효율화의 결과로 전체 생산량이 줄었기 때문"이라고 설명했다. 코로나19의 세계적 확산으로 주요 해외법인이 상반기에 셧다운(Shut down)된 상황도 수익성 악화의 요인으로 꼽았다. 다만 최근 글로벌 경제 회복에 맞춰 생산·판매활동이 재개되며 매출 및 수익성이 개선되고 있는 추세라고 밝혔다. 현대제철은 올해도 사업구조 효율화를 지속적으로 추진한다는 방침이다. 현대제철은 2020년 박판열연설비, 컬러강판설비 등 경쟁력이 떨어지는 부문에 대해 사업철수를 단행했다. 또 단조사업 부문을 분리시켜 단조전문 자회사 현대IFC를 출범시켰다. 현대제철은 콘퍼런스콜에서 "지난해 사업 조정을 하면서 단기순손실이 난 부분이 있지만 적자가 지속된 사업을 걷어내면서 올해부턴 플러스 요인으로 반영될 것"이라며 "올해도 판재류·봉형강 등 핵심 사업 외에 지속적으로 어려운 사업은 구조조정을 검토하겠다"고 밝혔다. 업비트 투자자 보호 센구조조정 대상 사업과 관련해선 "후판과 특수강은 주력 강종이고 긴 호흡으로 구조조정을 검토하는 사업"이라며 "시황에 의해 적자인 측면도 있고, 개선 과정에 있다"고 설명했다. 이어 "스테인리스 사업은 손익분기점(BEP)가 작년 수준을 유지 중"이라며 "구조조정 여부는 아직 결정 안 됐다"고 덧붙였다.미래 모빌리티 등과 관련한 사업 전망에 대해서도 언급했다. 현대제철은 "전기차에서 강판 자체의 사용량은 줄지 않을 것으로 보고, 초고장력강판 등 고급재 비율이 늘어나 수익성 측면에선 비슷할 것"이라고 밝혔다. 이어 "수소차용 연료전지 분리판은 사업 확장을 생각하고 있고, 물량이 늘어나면서 좋은 효과를 가져오지 않을까 생각한다"고 덧붙였다. 수소 사업과 관련해선 "부생가스 활용 부분은 큰 그림을 그려서 개발 계획을 추진하고 있고 부품 관련 부분은 수소 저장·운송 과정에서 필요한 부분에 따라 기초 연구를 실행할 것"이라고 말했다. 현대제철은 상반기 중 사업별로 조직체계를 운영하는 사업부제로 개편할 예정이다. 현대제철은 "책임경영제로 전체 흐름을 총괄하도록 구상하고 있다"며 "상반기 내로 내용을 확정해 공개하겠다"고 밝혔다. 현대제철은 철광석 가격에 대해선 2분기부터 안정화될 것으로 내다봤다. 현재 치솟은 철광석 가격 상승분을 고려해 자동차 및 조선업체와 협상 중이다. 가격 인상분을 기존 판매 물량에 소급 적용하는 방안도 추진한다. 현대제철은 "현대차·기아와 긍정적인 방향으로 가격 협상 중이고 조선사도 후판 가격 인상 협상을 진행하고 있다"며 "2021년 1~2분기 내 결론을 낼 수 있도록 노력할 것"이라고 했다.현대제철은 2021년 판매량 전망치를 1934만4000톤으로 제시했다. 이는 2020년 판매량 1967만8000톤보다 1.7% 감소한 물량이다. 이에 대해 현대제철은 "박판열연, 단조공장 등 사업구조 효율화로 생산 규모가 줄어들 것으로 예상한다"며 "줄어든 판매량만큼 고부가가치 제품 판매를 확대해 실적을 개선할 것"이라고 말했다. 아울러 2021년은 철강 본연의 제조경쟁력을 확보하겠다는 방침이다. 열연부문의 생산성을 향상하고 냉연설비를 신예화해 자동차강판의 생산성과 품질을 높인다. 자동차강판 시장 경쟁력 강화를 위해 신규강종 개발에도 집중 투자한다. 지난해 48종의 강종을 개발한데 이어 올해는 45개 강종을 신규 개발해 총 누계 311종의 자동차용 강종을 개발하는 것이 목표다. 2020년 개발 완료된 '9% Ni(니켈) 후판'의 양산체계를 구축함으로써 친환경 기조에 따라 수요가 확대되고 있는 LNG(액화천연가스) 추진선 및 LNG 저장시설 시장도 적극적으로 공략한다. ESG 활동도 적극적으로 추진해나간다. 탄소배출 감축을 위해 코크스건식소화설비(CDQ)에 대한 투자를 지속하는 한편, 그린본드 발행을 통해 마련한 재원으로 환경분야 투자를 확대한다. 2024년 설치 완료되는 CDQ설비가 가동되면 연간 50만 톤에 달하는 탄소배출 감축효과가 기대된다.[27]
현대차그룹의 수직계열화 구조에서 '철강 공급'을 맡고 있는 현대제철이 홀로서기에 나서고 있다. '현대차를 위한 강판 제조 기업'이라는 기존 인식에서 벗어나 자체적인 미래 성장동력을 확보하겠다는 목표다. 현대제철은 현대차그룹향으로 자동차 강판과 특수강 등을 공급하며 그룹의 한 축을 담당하고 있다. 글로벌 완성차 업체 가운데 자체 제철소를 보유한 브랜드는 현대차가 유일하다.현대차그룹은 현대제철(강판)-현대위아(부품)-현대모비스(생산라인)-현대글로비스(물류)-현대차(자동차제조)로 이어지는 수직계열화 구조를 가지고 있다. 이러한 구조는 안정적인 공급이 가능하지만 계열사의 제품 가격 인상을 제한하는 요인으로 꼽힌다. 현대제철의 2020년 실적은 수요산업이 하락하면서 판로를 확보하지 못해 대폭 감소했다. 매출액은 전년 대비 12.1% 감소한 18조234억원, 영업이익은 78% 감소한 730억원을 기록했다. 영업이익률은 2년 연속 1%를 밑돌았다. 그룹 내 수직계열화 분위기도 미묘하게 달라지고 있다. 정의선 회장이 취임하고 전기수소차, 도심항공(UAM), 로보틱스 등 미래 모빌리티 서비스로의 전환을 천명했기 때문이다. 그룹 입장에서 다량의 탄소를 발생시키는 제철 사업은 미래 모빌리티 비전과 상반된다. 정 회장은 지난해 임기 만료 1년을 앞두고 현대제철 사내이사직에서 중도 사임했다. 2012년 사내이사로 오른 이후 8년 만이다. ‘쇳물에서 차까지’로 대표되는 수직 계열사의 경영보다 그룹 핵심인 미래 모빌리티에 더욱 집중하겠다는 의지를 나타낸 셈이다. 동시에 현대제철을 이끌고 있는 안동일 사장의 경영전략에 대한 기대감과 부담감도 높아지고 있다. 2019년 취임한 안 사장은 포스코 광양제철소장과 포항제철소장 등을 역임해 제철 설비와 생산분야 전문가로 평가 받는다. 안 사장의 경영 키워드는 ‘수익성 중심의 철강사’다. 현대제철은 2020년 노조와의 협의 끝에 경쟁력이 낮은 박판열연설비, 컬러강판설비 등의 사업을 철수했다. 컬러강판라인(CCL)은 타 제강사 대비 노후한 설비 등으로 매년 100억원 이상의 적자를 내는 사업부였다. 이어 단조사업 부문을 분리시켜 단조전문 자회사 현대IFC를 출범해 철강 본연의 사업성을 높이는 데 주력했다. 또 다른 전략은 전기차 시대에 맞는 자동차용 강종 개발이다. 현대제철은 매년 신소재 개발을 위해 1100~1400억원을 투자하고 있다. 2020년에는 자동차용 신제품 6건을 출시했다. 현대제철은 2020년까지 266종의 자동차 강종을 개발했으며 자동차 강종 커버리지를 74%까지 높인다는 방침이다. 내부거래 비율은 점차 줄어드는 추세다. 현대차그룹과의 내부거래 비율은 2016년 19.1%에서 2020년 16.8%로 2.3%포인트 감소했다. 업계의 한 관계자는 “현대차그룹의 수직계열화 분위기가 예전 같지 않다”며 “현대제철의 자체 경쟁력이 요구되는 만큼 신소재 개발과 글로벌 완성차 업체로의 판로를 확보하는데 주력할 것”이라고 설명했다. 한편 1분기 실적은 체질 개선에 힘 입어 반등이 예상된다. 증권가는 현대제철의 1분기 별도 기준 영업이익을 전년 동기 대비 350% 상승한 1600억원으로 추산하고 있다.권순우 SK증권 연구원은 “올해 311종의 강종 개발이 완료되면 공급능력이 강화되고 이미 개발한 핫스팸핑과 초고장력강을 기반으로 외부시장의 비중이 늘어날 것”이라며 “현대차그룹의 전기차 전용 플랫폼인 'E-GMP' 생산이 시작되면 가치 개선도 이뤄질 것"이라고 평가했다.[28]
현대제철이 글로벌 경제 회복세에 힘입어 실적 개선에 성공했다. 현대제철은 2021년 4월 27일 연결기준 1분기 매출 4조9274억원, 영업이익 3039억원을 기록했다고 공시했다. 매출액은 전년 동기 대비 5.6% 올랐고, 영업이익은 흑자전환했다. 영업이익률은 전년인 2020년 대비 6.2% 늘어 적자를 벗어났다. 이 같은 실적 반등은 글로벌 철강 시장이 개선되면서 판재류 중심으로 제품가격이 인상됐고, 고부가 제품의 판매가 확대됐기 때문이라고 현대제철은 설명했다. 실제 국내 열연과 후판은 조선·자동차 등 주요 수요산업의 업황개선과 중국의 철강재 감산기조의 영향으로 100만원 초반대 가격을 형성하고 있다. 현대제철은 1일 업무 효율성을 높이기 위해 사업부제를 도입했다. 기존 기능별 조직체계을 혁신해 고로, 전기로 등 사업 단위로 조직체계를 전환했다. 이를 통해 의사결정 과정을 간소화하고 시장과 고객의 요구를 신속하게 대응한다는 전략이다. 연구개발 부문은 전기차 차체부품용 1.5GPa급 초고강도 냉연강판과 영하196℃ 극저온을 버틸 수 있는 9% Ni(니켈)강을 개발하는 등 성과를 냈다. 연구개발팀은 현재 LNG 선박 연료탱크와 LNG 육상 저장 탱크에 공급을 추진 중이다.이에 현대제철은 글로벌 자동차강판 판매 목표를 기존 69만톤에서 82만톤으로 높게 설정했다.현대제철은 신설 통합수주관리 조직을 신설해 사회간접자본(SOC) 수주를 강화한한다. 아울러 조선·자동차 산업을 겨냥해 고부가 제품 판매를 늘릴 계획이다. 특히 글로벌 자동차 시장의 전기차 전환 추세에 맞춰 경량화 소재에 대한 증설 투자를 계획하고 있다. 회사는 2023년 3월까지 체코 법인의 핫스탬핑 라인의 증설을 완료해 기존 320만 매(枚) 생산규모를 480만 매로 확대할 계획이다. 현대제철은 "철강 시황의 상승이 계속되고 있어 원자재가격 상승분을 제품 가격에 반영해 수익성을 개선할 것"이라며 "주요 수요처별 맞춤형 영업활동을 전개하고 마케팅 활동을 강화할 것"이라고 말했다.현대제철은 이날 컨퍼런스콜을 통해 "글로벌 기업평가 기준인 ESG(환경·사회·지배구조) 경영을 위해 노력을 기울이고 있다"고 설명했다. 특히 이사회 구성원의 다양성을 높이고 운영의 독립성을 확보했다. 현대제철은 2021년 3월 주주총회에서 장금주 서울시립대 경영학 교수를 사외이사로 선임했다. 장 교수는 세금 관련 논문을 집필하는 등 회계·세무 분야 전문가로 알려져 있으며 한국윤리경영학회 수석부회장을 겸임하고 있다. 이번 결정은 사외이사를 통해 윤리경영을 강화하겠다는 현대제철의 의지로 풀이된다. 현대제철이 여성 사외이사를 선임하는 것은 창립 이후 처음이다. 이어 제철 사업의 태생적 한계를 극복하기 위해 탄소 감축에 동참하고 있다고 밝혔다. 현대제철은 올해 들어 국내 철강업계 최초로 녹색채권을 발행해 4900억원 규모의 재원을 마련했다. 2020년 12월에는 대기오염물질 감축을 위해 세계 철강사 최초로 가스청정밸브를 개발해 3개의 고로에 설치 완료했다. 노사는 2020년 임금단체협약(임단협)을 타결해 ESG경영 중 사회(S) 분야의 과제를 해소했다. 현대제철 노조 5개 지회는 기본급을 동결하되, 2호봉 정기승호 시에 2만3000원을 지급하는 등 조건으로 협상안을 찬성했다. 현대제철은 해를 넘기고도 2020년 임금단체협약을 타결하지 못 했지만, 꾸준히 협상을 진행해 노조의 합의를 이끌어 냈다.[29]
전망
현대차의 순수 전기차 '아이오닉5'가 출시되면서 전기차용 특수강을 개발하고 있는 현대제철과의 시너지 효과에 관심이 모이고 있다. 현대차는 자체 제철소를 보유한 유일한 완성차 업체로서 현대제철과의 협력을 강화한다는 전략이다. 2021년 3월 4일 업계에 따르면 현대제철은 현대차의 전기차 전용 플랫폼 E-GMP(Electric-Global Modular Platform)를 위한 특수강 소재를 개발하고 있다. E-GMP 플랫폼에서 현대제철이 생산하던 기존 내연기관의 엔진과 변속기는 구동모터와 감속기로 대체된다. 전기차의 특수강 소요량은 내연기관 자동차 대비 약 20% 수준으로 감소한다. 다만 전기차 판매량이 증가하면서 특수강 소요량은 현재 수준과 비슷할 것으로 보인다. EGMP 기반 전기차는 특수강 소재와 강판, 배터리 케이스를 필요로 한다. 특히 전기차는 배터리 무게 비중이 높아 차체가 가벼워질 수 밖에 없다. 따라서 안정성이 필수과제로 꼽힌다. 현대제철은 기존 알루미늄 배터리 케이스를 대체해 철 소재를 사용한 스틸 배터리 케이스를 개발했다. 스틸 배터리 케이스는 알루미늄 배터리 케이스와 비교해 무게는 비슷하지만 원가는 15%가량 낮다. 또한 알루미늄보다 내연성과 안전성이 높은 것이 특징이다. 현대제철은 스틸 배터리 케이스를 미래 먹거리로 보고 있다. 테슬라, BMW, 아우디 등 글로벌 완성차 업체는 90% 이상 알루미늄 배터리 케이스를 쓰고 있어, 스틸 배터리 케이스로 대체할 경우 시장을 선점할 수 있다. 현대제철은 차세대 스틸 배터리 케이스를 현대차의 차세대 모델에 적용하기 위한 테스트를 진행 중이다. 또한 매년 연구개발에 1100~1400억원을 투자하는 등 신소재 개발에 힘을 쏟고 있다. 2020년에는 자동차용 신제품 6건을 출시했다. 회사는 2020년까지 266종의 자동차 강종을 개발했으며 자동차 강종 커버리지를 74%까지 높인다는 방침이다. 현대차그룹은 미래 모빌리티 전환을 목표로 플랫폼 구축과 소재 개발을 협력해 시장을 공략에 나서고 있다. 현대차는 글로벌 시장을 겨냥해 전기차 플랫폼인 E-GMP를 완성하고, 현대제철은 특수강과 부품 소재를 개발해 경쟁력을 강화한다. 현대차그룹은 세계에서 유일하게 자동차용 특수강을 생산하는 현대제철을 자회사로 두고 있다. 대부분의 완성차 업체가 제철사로부터 철강을 제공받는 것과 달리 제품 개발과 소통 면에서 강점을 갖는다. 토마스 뷔르클레 현대차 유럽 디자인센터장은 2021년 2월 23일 탑기어와의 인터뷰에서 "현대차그룹은 철을 자체 생산하는 유일한 자동차 회사"라며 "따라서 우리는 더욱 정밀한 정밀도를 확보할 수 있다"고 말했다. 앞서 현대제철은 현대차와 함께 차체 무게를 줄여 연비를 개선시키는 'TWB 핫스탬핑 차체부품용 1GPa' 소재를 개발했다. 1GPa는 1mm x 1mm 크기의 재료가 100kg을 버틸 수 있는 강도로, 기존 자동차 외부 판재 대비 2~5배 강한 수준이다. 이 소재는 외부 충돌에 버티는 차량 뼈대 역할을 맡는 센터필러 제조에 쓰이며 경량화와 고강도가 필요한 전기차에서 탑승자의 안전을 확보할 수 있는 기술로 평가 받는다. 2019년 출시한 '아이오닉 하이브리드'에도 이 소재가 적용됐다.현대제철은 현대차를 포함해 자동차 향으로 연간 약 550만톤 이상을 공급하고 있다. 현대제철은 내년까지 개발을 완료한 전기차용 특수강과 강판의 공급 기반을 구축한다는 계획이다. 현대제철 관계자는 "현대차와의 협력과정은 피드백이 원활해 제품 개발과 개선을 신속하게 진행할 수 있는 장점이 있다"고 설명했다. 한편 아이오닉5는 현대차가 자체 개발한 전기차 전용 플랫폼 E-GMP가 적용된 최초의 모델이다. 현대차그룹은 아이오닉5를 시작으로 기아CV, 제네시스JW, 아이오닉6, 아이오닉7 등 전기차 모델을 출시할 예정이다.[30]
연간 125만톤의 철근 생산 능력을 갖춘 현대제철 철근공장이 당분간 가동을 멈추며 국내 철근 수급 상황에 긴장감이 더해질 것으로 전망된다. 고용노동부에 따르면 고용노동부 천안지청은 지난 2021년 5월 8일 현대제철 당진제철소에서 사망사고가 발생한 이후 감독관을 파견해 사고 조사를 실시했다. 이후 사고가 발생한 1열연 3호기 가열로 작업에 대해 구두 작업중지를 명령했다. 이어 천안지청은 2021년 5월 10일 지청장과 과장 등이 현대제철 당진제철소에 방문해 작업중비 범위 및 급박한 산재발생 위험 정도를 추가적으로 조사했으며, 1열연공장 0,3호기 가열로, 철근공장 가열로 작업에 대해 작업중지를 명령했다. 고용노동부는 "산업안전감독 실시, 안전보건진단 명령 및 트라우마 치료 등 산업안전 확보를 위한 가능한 조치를 다 할 계획이다."라고 설명햇다. 고용노동부가 현대제철 당진 철근공장의 작업을 중지하게 함으로 인해 국내 철근 수급 상황은 더욱 빡빡함을 유지할 것으로 예상된다. 특히 현대제철 당진 철근공장에 대한 작업중지 명령의 종료시점이 발표되지 않아 수급 긴장감은 당분간 이어질 것으로 보인다. 철강업계에 따르면 2021년 국산 철근 재고는 10만톤 중반대를 형성하고 있다. 통상 국산 철근 재고는 25만 ~ 30만톤 수준을 적정재고라고 평가해왔으나, 2021년 제품 시황 개선과 건설 등 수요 산업 업황 회복의 영향으로 출하량이 늘어나 재고 또한 낮은 수준을 형성하고 잇다. 이에 현대제철 등 대부분의 철근 제조업계가 제품 생산에 열을 오리고 있으나, 실제 수급 상황은 빡빡함을 유지하고 있으며 제품 유통가격 또한 강세를 나타내고 있다. 더욱이 5~6월 계절적 성수기 기간 동안 제품 수요가 늘어나는 것의 영향을 받아 제품 수급 상황은 긴장감을 당분간 이어갈 것으로 예상된다. 한편 현대제철 당진 철근공장은 연간 125만톤, 일간 3,500톤 수준의 제품 생산 능력을 갖추고 있다.[31]
국내 철강업계가 중국발 겹호재를 만나 실적 기대감이 상승하고 있다. 2분기 역대급 실적에 이어 하반기에도 강세가 점쳐지면서 미소를 짓는 모습이다. 2021년 8월 8일 업계에 따르면 중국 정부는 2021년 8월 1일부로 냉연도금재·아연도강판 등 23개 철강 제품에 대한 수출증치세 환급을 폐지했다. 2021년 5월 열연·후판 등 146개 품목에 대한 수출증치세 환급 폐지에 이은 추가 조치다.증치세는 중국 철강사들이 철강재를 수출할 때 부과하는 부가가치세다. 중국 정부는 13% 가량의 증치세를 환급해주며 수출을 장려해왔다. 하지만 전 세계적인 탄소저감 기조에 따라 정책이 바뀌었다. 중국은 2060년까지 탄소중립 달성 목표에 따라 수출 혜택을 중단하고 생산물량을 내수로 돌리고 있다. 2021년 조강 생산량을 2020년 수준(10억6000만t)으로 유지한다는 목표다. 또 중국은 철강제품에 수출 관세를 부과하는 방안도 고려 중인 것으로 전해졌다. 2021년 일부 외신은 중국 정부가 올 3분기 중 열연을 포함한 철강재에 10~25%의 관세를 부과하는 방안을 검토하고 있다고 보도했다. 수출증치세 환급 폐지에 이어 수출 관세가 부과될 경우 중국산 철강재의 가격 경쟁력이 크게 떨어질 것으로 전망된다. 업계에서 국내에 저가 중국산 제품이 줄어들고 국산 철강재 선호도가 증가할 것이란 관측이 나오는 이유다. 게다가 중국의 감산 정책에 따른 수요 둔화 우려에 원자재인 철광석 가격이 내려가고 있는 점도 국내 철강사들에 희소식이다. 산업통상자원부 원자재가격정보에 따르면 2021년 7월 30일 기준 철광석 가격은 톤당 181.57달러로 집계됐다. 톤당 180달러대는 2021년 5월 이후 3개월 만이다. 원자재값 하락은 자동차‧조선‧건설 등 전방산업 수요가 넘쳐 철강재 가격 강세가 유지될 가능성이 높은 가운데 수익성 개선 효과로 이어질 전망이다.이같은 호재들에 힘입어 국내 철강업계는 하반기에도 깜짝 실적을 보일 가능성이 커졌다. 지난 2분기 놀라운 성적을 거둔 철강사들이 3분기에 이를 능가하는 호실적을 낼 것이란 관측도 나온다. 대표적으로 포스코와 현대제철은 2분기 영업이익이 각각 2조2000억원, 5453억원에 달하며 역대급 실적을 기록했다. 포스코는 2분기 실적발표 컨퍼런스 콜에서 “반도체 수급이슈 정상화로 자동차향 수요가 반등하는 한편 조선·가전 등 전체적으로 수요 강세가 지속될 것”이라며 “중국에서 탄소중립을 위해 감산을 유도하고 있고, 철강 시장 안정화를 위해 수출을 억제하고 있는 등 국내의 타이트한 수급 상황이 지속되며 하반기 긍정적인 실적을 예상하고 있다”고 밝혔다.[32]
각주
- ↑ 〈현대제철〉, 《나무위키》
- ↑ 2.00 2.01 2.02 2.03 2.04 2.05 2.06 2.07 2.08 2.09 2.10 2.11 2.12 2.13 2.14 2.15 2.16 2.17 2.18 2.19 2.20 2.21 2.22 2.23 2.24 2.25 2.26 2.27 2.28 2.29 〈현대제철〉, 《현대제철》
- ↑ 3.0 3.1 3.2 3.3 남희현 기자, 〈(Who Is ?) 안동일 현대제철 대표이사 사장〉, 《비즈니스포스트》, 2019-05-13
- ↑ 이한재 기자, 〈(Who Is ?) 안동일 현대제철 대표이사 사장〉, 《비즈니스포스트》, 2021-03-15
- ↑ 김덕수 기자, 〈현대제철 제1고로 화입, 희망의 불꽃을 피우다〉, 《한국건설신문》, 2010-01-05
- ↑ 김덕수 기자, 〈현대제철, 고로 조업 첫 분기 흑자 달성〉, 《한국건설신문》, 2010-07-30
- ↑ 7.0 7.1 7.2 7.3 김덕수 기자, 〈현대제철 3고로 화입, 대한민국 산업에 새로운 심장이 뛴다〉, 《한국건설신문》, 2013-09-16
- ↑ 김태완 기자, 〈현대제철, 고로 유해가스 배출 원천차단 기술개발 성공〉, 《머니투데이》, 2020-12-22
- ↑ 김종선 기자, 〈현대제철,국내 최초 전기로 210mm 슬래브 생산〉, 《인터넷 환경일보》, 2007-06-14
- ↑ 서의규 기자, 〈전기로제강 최초 400규격 극후 H형강 개발 성공〉, 《철강금속신문》, 2008-09-30
- ↑ 한종해 기자, 〈현대제철, 빅데이터 기반 전기로 원료 운영 최적화 시스템 구축〉, 《파이낸셜 투데이》, 2020-04-28
- ↑ 김준 기자, 〈현대제철·하이스코 합병 ‘자산 31조’ 제철소로〉, 《경향비즈》, 2015-04-08
- ↑ 김명득 기자, 〈현대제철, 돈 되는 강관사업으로 활로 모색〉, 《경북매일》, 2018-01-18
- ↑ 서동철 기자, 〈(단독) 현대제철, 실적부진 강관사업 매각 나선다〉, 《경북매일》, 2020-01-03
- ↑ 콘텐츠부, 〈현대제철, 글로벌 자동차 소재 공급 확대 및 경쟁력 강화 집중〉, 《조선비즈》, 2020-03-30
- ↑ 유범종 기자, 〈현대제철, 올해도 사업재편 안 놓는다〉, 《팍스넷뉴스》, 2021-01-28
- ↑ 17.0 17.1 17.2 현대제철, 〈친환경 제철소로 변신 중인 현대제철〉, 《현대자동차그룹》, 2021-04-13
- ↑ 18.0 18.1 신준혁 기자, 〈탄소 빼고 '수소'로 채웠다... 현대제철, 친환경 기업 대변신〉, 《시장경제》, 2021-07-01
- ↑ 신준혁 기자, 〈'ESG·준법경영' 대대적 변화... 현대제철, '기업체질' 확 바뀐다〉, 《시장경제》, 2021-02-26
- ↑ 옥승욱 기자, 〈현대제철, 'ESG 정보공개'로 美 LACP 비전 어워즈 금상〉, 《뉴데일리》, 2021-03-03
- ↑ 정석만 기자, 〈현대제철, 극저온 견디는 후판 개발…"친환경 LNG 시장 공략"〉, 《아시아투데이》, 2021-02-09
- ↑ 이성은 기자, 〈현대제철, 전사 클레임 캠페인 추진…소비자 '불만제로' 시동〉, 《신아일보》, 2021-02-01
- ↑ 권오은 기자, 〈현대제철, 엔투비와 MRO 구매대행 협약… 사회공헌기금도 조성〉, 《조선비즈》, 2021-07-18
- ↑ 이수영 기자, 〈현대제철, 버려진 조개껍데기로 쇳물 뽑는다〉, 《프라임경제》, 2021-07-28
- ↑ 송영훈, 〈33명의 죽음, 잊었나…되풀이 되는 현대제철 사고〉, 《노컷뉴스》, 2019-02-21
- ↑ 강예슬, 〈(자회사냐, 해고냐 택일?) 현대제철 사내하청업체 14곳 폐업통보〉, 《매일노동뉴스》, 2021-08-03
- ↑ 최민경, 〈현대제철 지난해 영업익 78%↓…"구조 개편·고부가 사업으로 극복"〉, 《삼성》, 2021-01-28
- ↑ 신준혁, 〈현대제철, 脫수직계열화 속 독자 경쟁력 강화〉, 《시장경제》, 2021-03-19
- ↑ 신준혁, 〈현대제철, '0%' 오명 씻는다... 1Q 영업익 3039억〉, 《시장경제》, 2021-04-27
- ↑ 신준혁, 〈'현대차' E-GMP에 '현대제철' 강판... 그룹 시너지 극대화〉, 《시장경제》, 2021-03-05
- ↑ 이형원, 〈현대제철 당진 철근공장 작업중지...수급 긴장감 고조〉, 《철강금속신문》, 2021-05-11
- ↑ 김명현 기자, 〈철강업계, 중국發 겹호재에 ‘미소’〉, 《매일일보》, 2021-08-08
참고자료
같이 보기